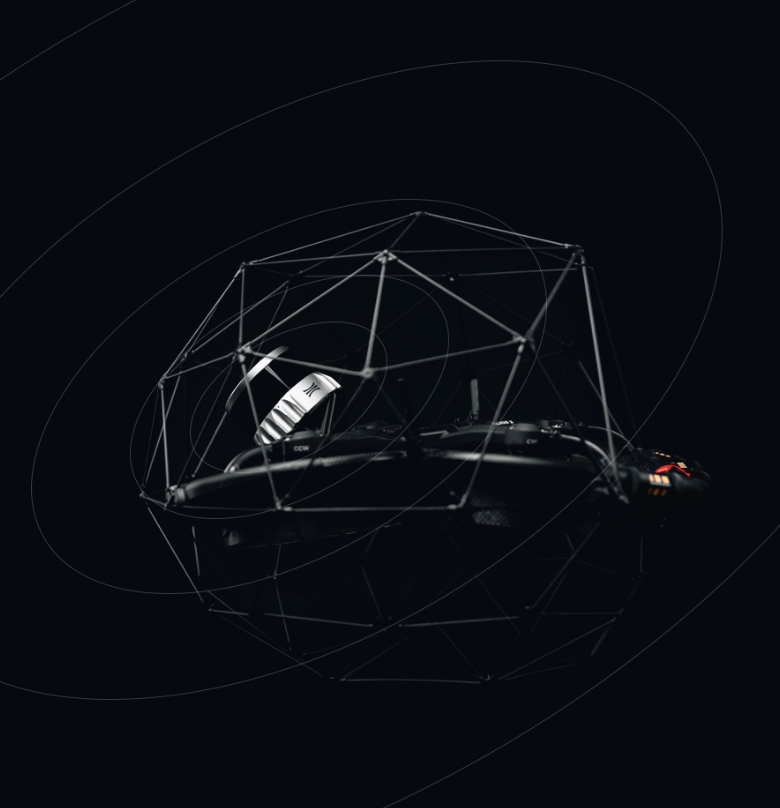
Bridge data gaps in challenging environments
Comprehensive data is key to supporting operational decisions. Yet many hazardous environments are beyond the reach of existing data capture technologies.
Flyability's Surveying Payload turns the Elios 3 into a flying mobile scanner that can fit through openings as small as 50x50cm, and create high resolution scans beyond line of sight, allowing industry professionals to provide rapid insights that are not accessible with traditional tools or other UAV technologies.
Survey-grade accuracy
The high resolution Ouster OS0-128 Rev 7 LiDAR sensor in combination with the world's leading FARO Connect SLAM algorithm create incredibly accurate 3D maps and digital twins of the most inaccessible spaces with centimeter precision - for accurate measurements and greater insights.
Accuracy
From 0.1%
drift
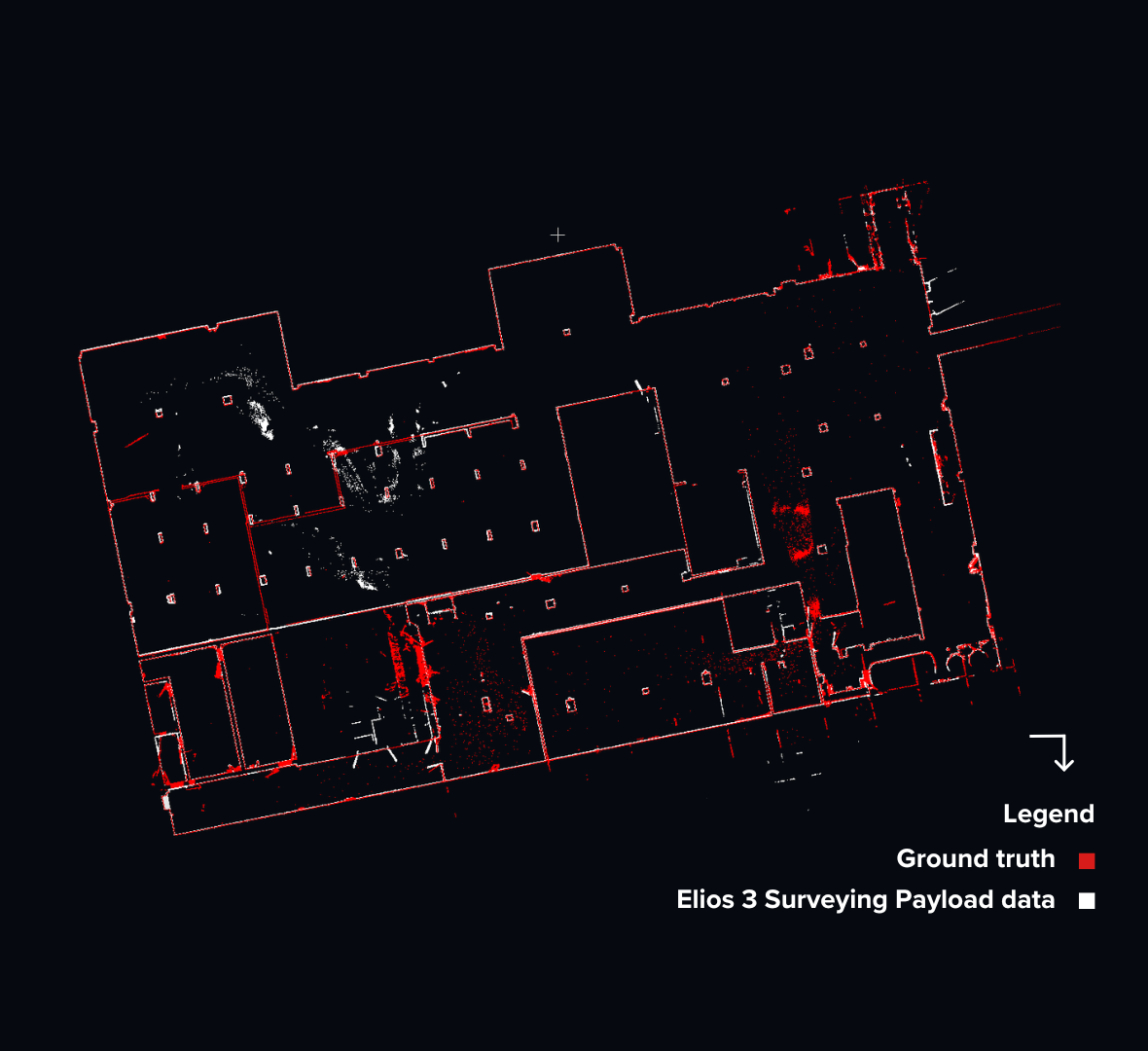

New mapping capabilities
Powered by the latest Ouster REV 7’s supercharged L3 chip, the Elios 3 has the ability to capture points further apart and to detect more usable visual features. This maximizes the chance for the SLAM algorithm to converge when computing 3D models of cylindrical and symmetrical environments such as collectors, chimneys, culverts, or underground galleries.
*Accuracy may vary depending on the geometry of the mapping environment. Read our detailed accuracy report to further assess the technology fit for your use case.
Stunning point clouds
Capture rich, detailed point clouds of the most complex indoors, operating from a safe location. With Elios 3’s Surveying Payload you can effortlessly create comprehensive visual representations of challenging indoor spaces, allowing for precise mapping and analysis.
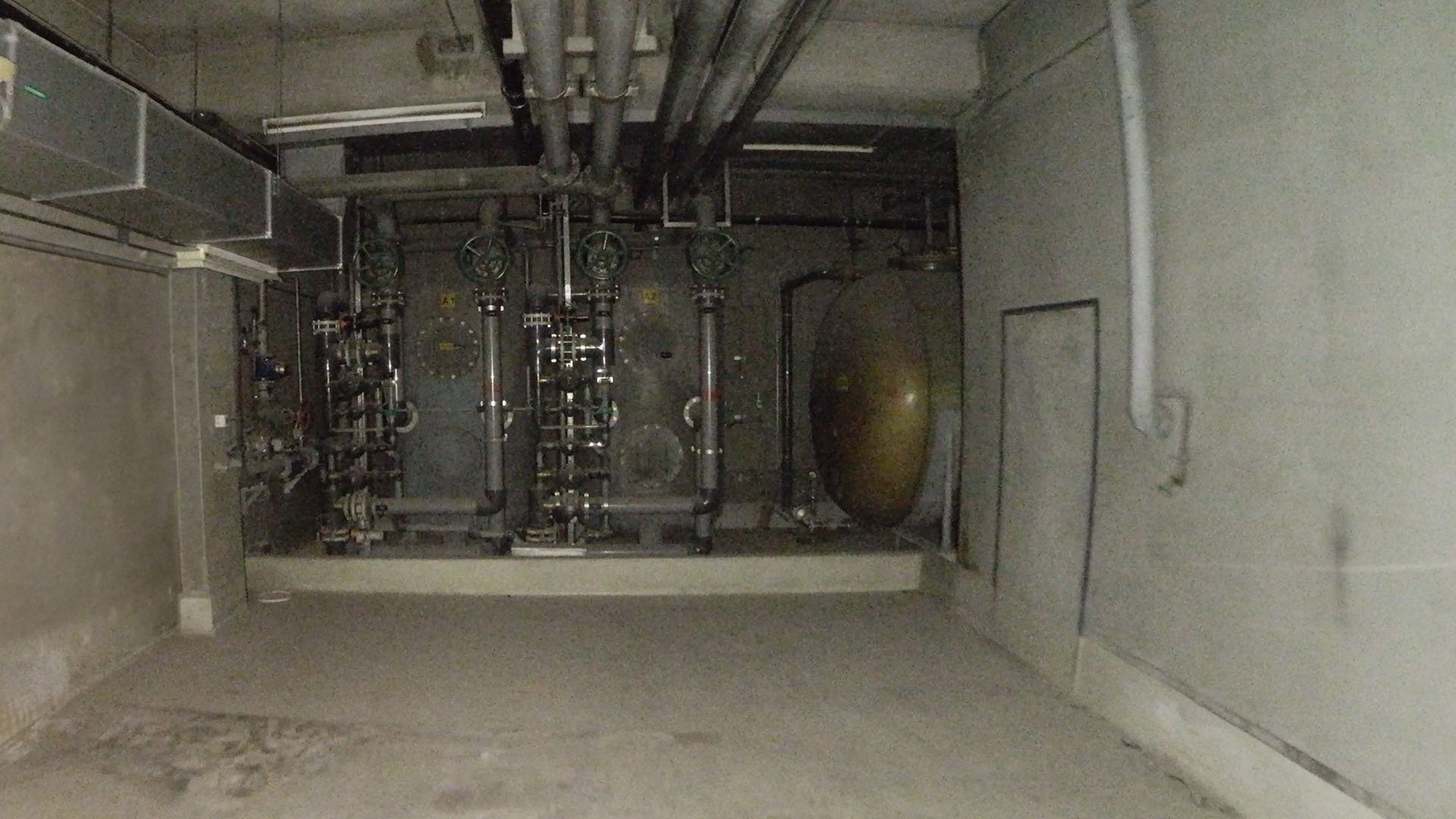
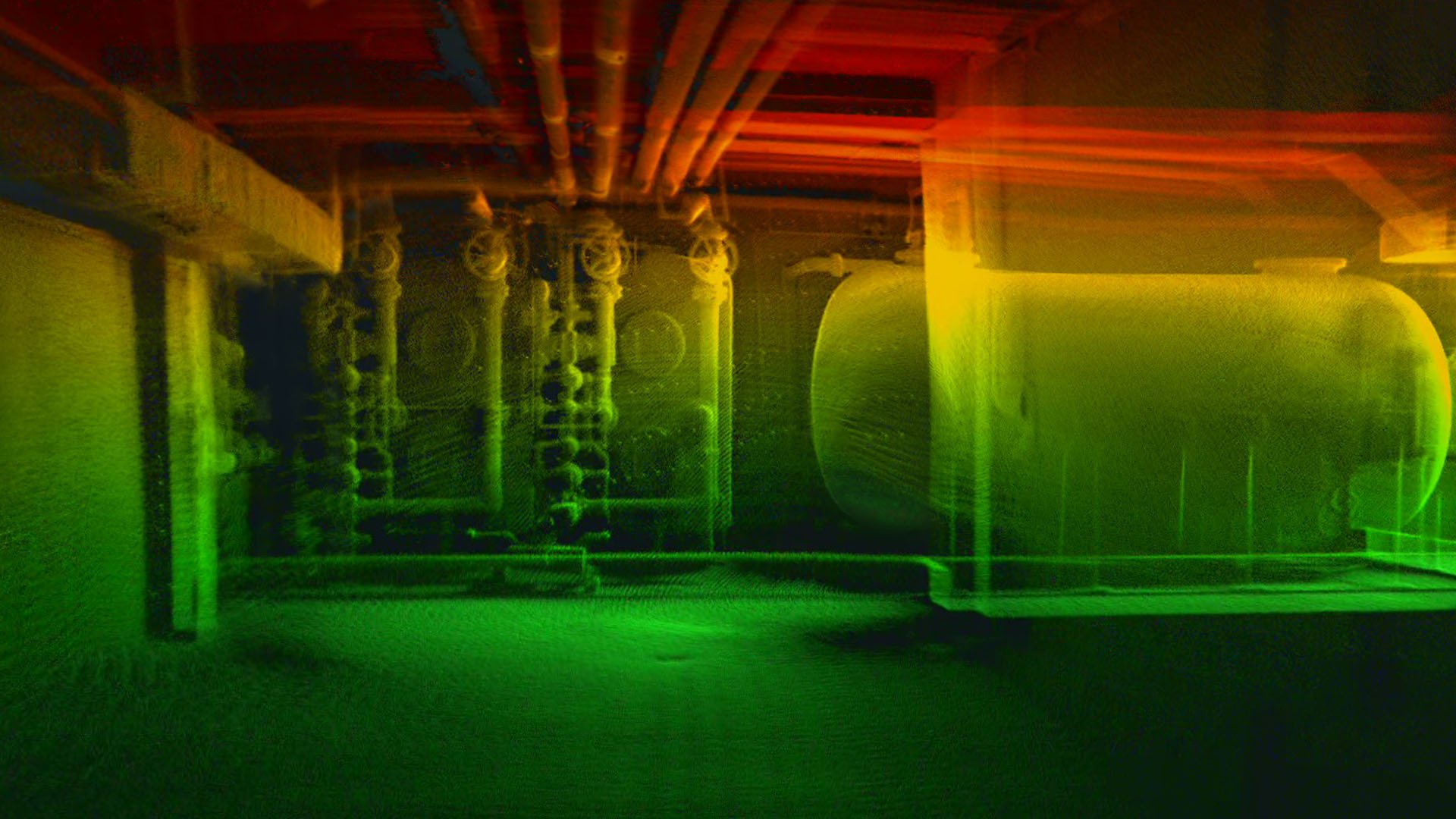
Precision 1σ
+/- 6 mm
Precision 2σ
+/- 12 mm
Photon Sensitivity
10 x
Uplifted mapping efficiency
For all applications where centimeter accuracy matters, mobile scanning is far more effective than traditional methods such as total stations or terrestrial scanners. With a range of 100 meters, a point density of 1,310,720 pts/sec and a capacity to cover a 300 meters tunnel (close loop) in a single flight, the Elios 3 Surveying Payload can turn days of mapping into a 10-minute job.
Range
Up to 100 m
Scanning rate
1,3 M pts / sec
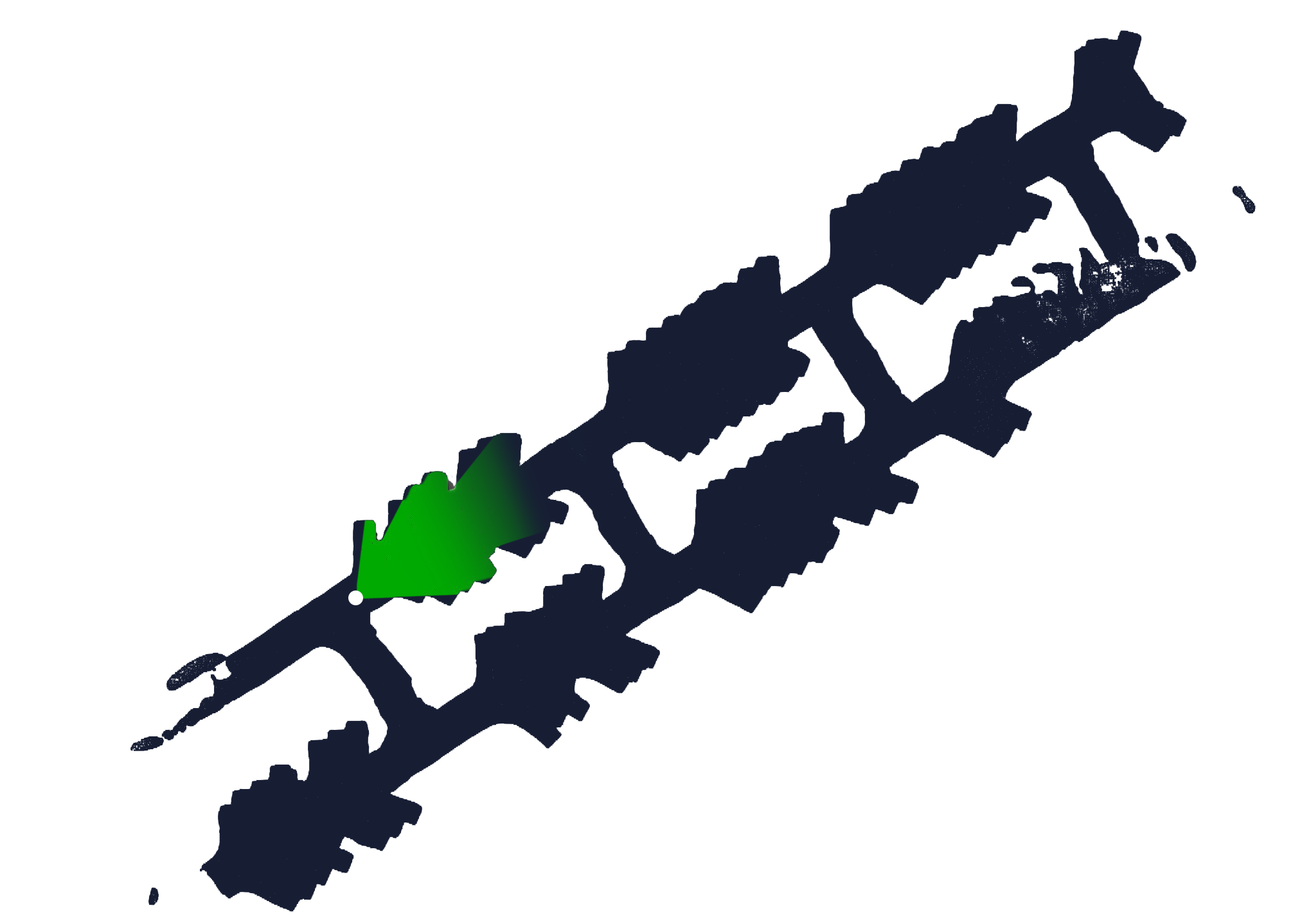
Terrestrial scan
Time: 18 minutes, Coverage: 15%
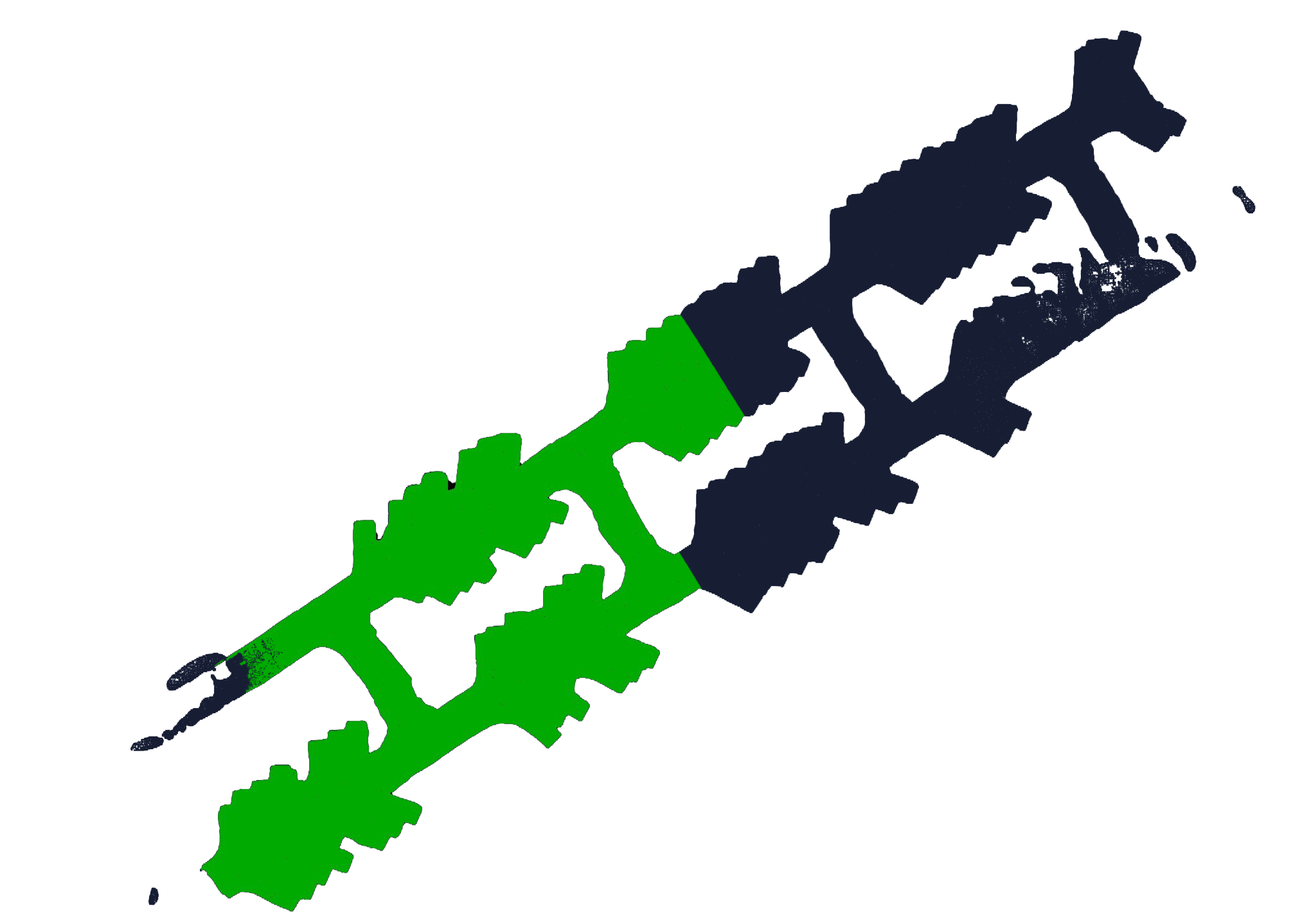
Elios 3 standard LiDAR configuration
Time: 18 minutes, Coverage: 50%
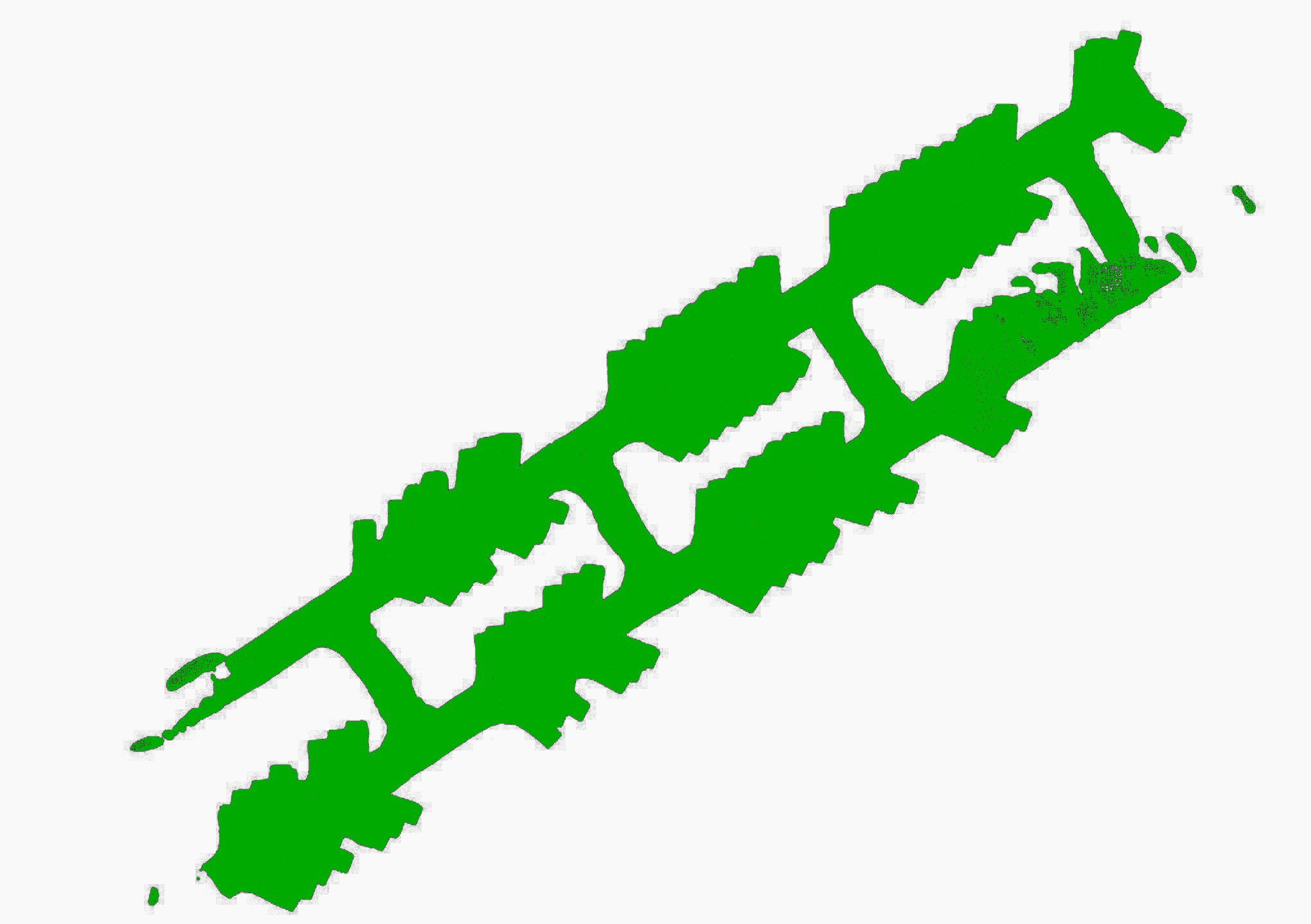
Elios 3 Surveying Payload
Time: 18 minutes, Coverage: 100%
Scanning beyond safe access
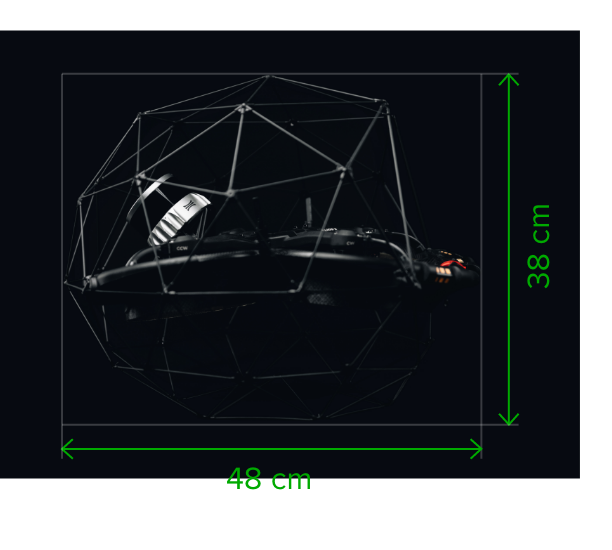
With its small form factor, the Elios 3 and the Surveying Payload can fit through openings as small as 50x50cm. It has a fixed cage that physically protects the hardware and a patented combination of flight controller and motor design that allows the drone to recover flight stability after a collision. This enables the drone to navigate through the most complex environments to capture high resolution scans where no other technology can.
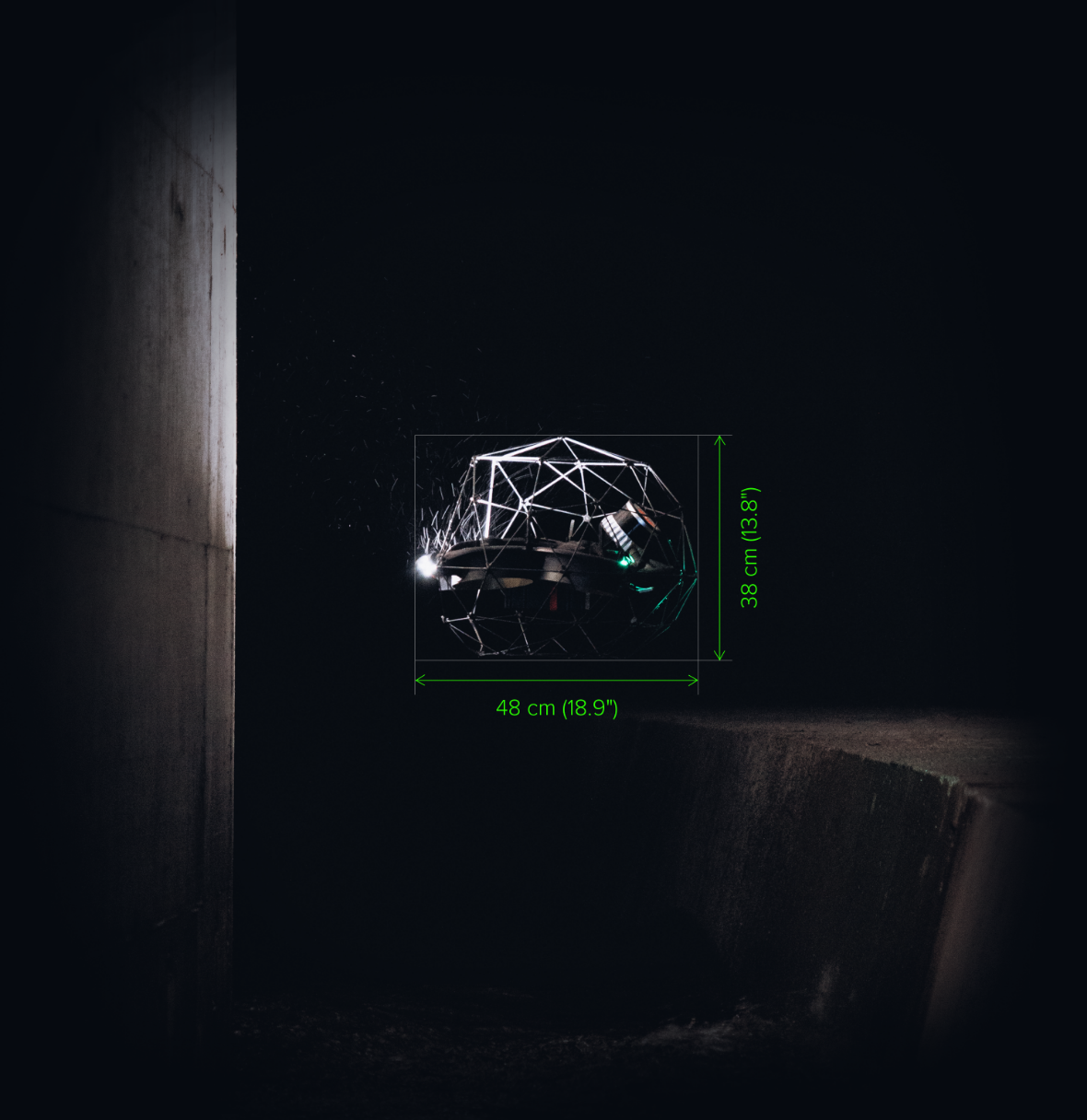
Software
Create clean, georeferenced point
clouds automatically
The Elios 3 Surveying Payload is bundled with FARO Connect, a powerful software solution to process and manage the Elios 3’s LiDAR data. Powered by the world’s leading SLAM algorithm, FARO Connect converts data from the Elios 3 into highly accurate point clouds and provides a range of SLAM presets, optimized for the most common data capture scenarios of the Elios 3. Features include:
Point cloud filtering
Refine Elios 3 3D models with various filters including outlier removal, surface noise reduction, and removal of unwanted points.
SURVEYING PACKAGE
A one-stop solution
To get you started, the Surveying Payload comes as a comprehensive package, which includes:
The hardware
The surveying payload comes as a package with the Elios 3 drone or as a standalone payload for existing Elios 3 users.
The FARO Connect software
This software is meant to ease the processing and management of Elios 3's LiDAR data.
A set of reflective targets
Perfectly sized for FARO Connect to automatically detect in the SLAM registration workflow.
An in-depth training course
Covering everything from best flight practices to processing and registration.
This package is designed to maximize your field experience and accelerate your operational proficiency.
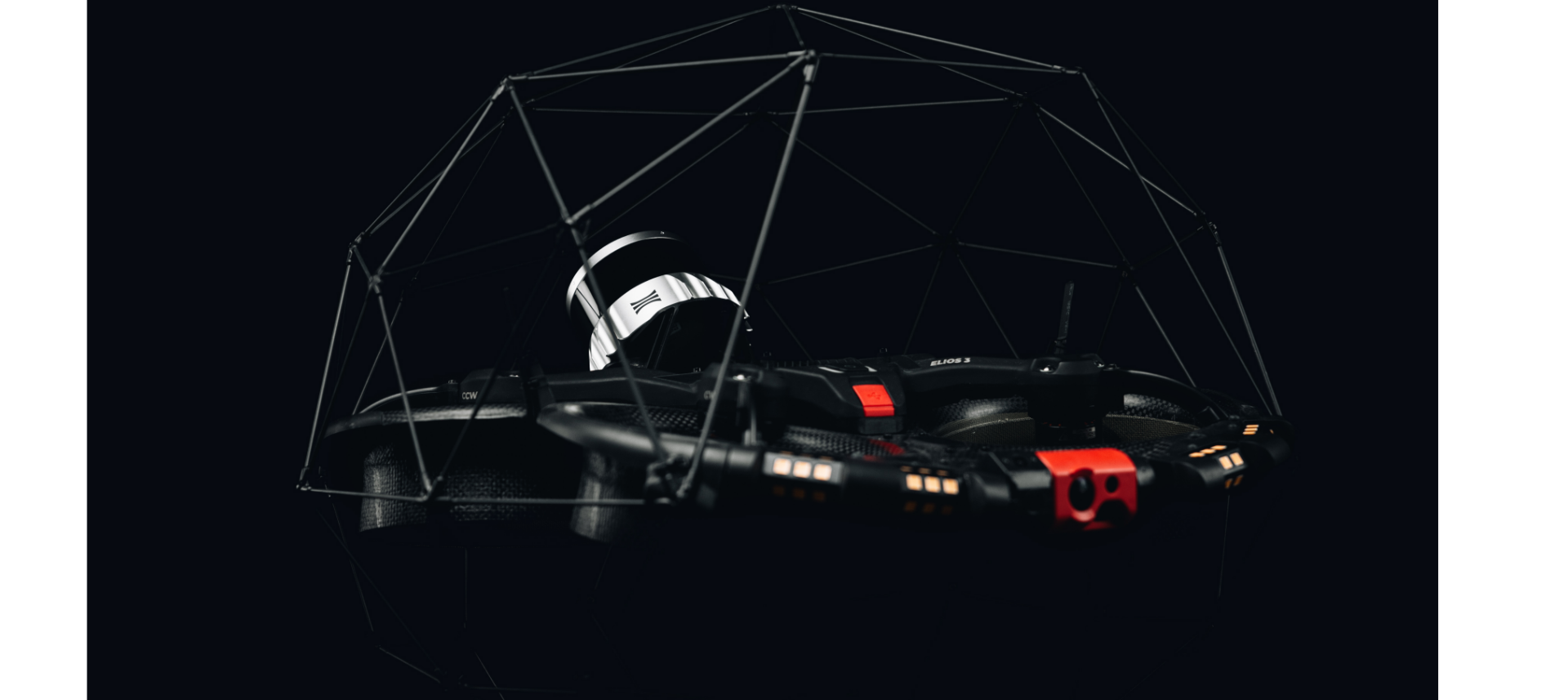
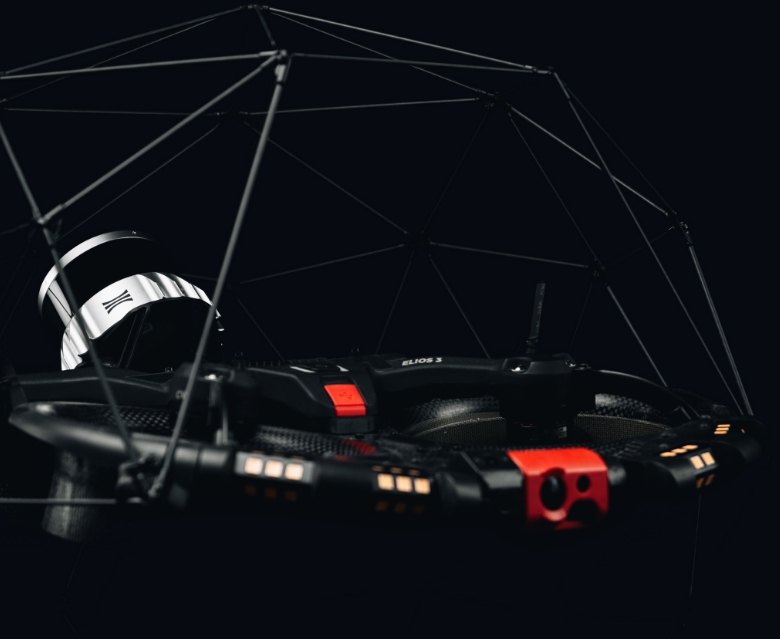
Elios 3 LiDAR configurations
The Elios 3 offers 2 LiDAR configurations. To help you determine if the Surveying Payload is right for you, you can refer to the table below, showing a concise overview of the key disparities between the two configurations.
Datapoint
Elios 3 & FlyAware
Elios 3 Surveying & FARO Connect
When localizing inspection data matters
When the 3D model matters
Range
1x
Up to 50m @ 80% reflectivity
Up to 15m @10% reflectivity
2x - 2.3x
Up to 100m 80% reflectivity
Up to 35m at 10% reflectivity
Precision (2 sigmas)
1x
+/- 1.8 cm
1.5x
+/- 1.2 cm
Accuracy
Some artifacts, like “wall collapses” or “double walls”
No artifacts as long as mapping guidelines are followed
in structured environments
1x
0.5-1% drift
5-10x
~0.1-0.2% drift
in nominal symmetric environments (>2m diameter, enough geometrical features)
1x
~2% drift
5-10x
~0.25-0.5% drift
in challenging symmetric environments (>2m diameter, little geometrical features)
1x
2-5% drift
4-5x
0.5-1% drift
in very challenging symmetric environments (<2m diameter, enough geometrical features)
1x
5+% drift
1-2x
2-5% drift
Points / sec
1x
~50k
25x
~1.3M
Light sensitivity
1x
10x
Mapping algorithm
Real-time SLAM focused on robustness, running on drone
Post-processing SLAM, focused on high accuracy, on desktop PC
Desktop software
Inspector (for reporting and data localization)
Inspector + FARO Connect (for georeferencing, 3D manip., etc)
Flight time, max altitude
9’ 30”, 3’000m AMSL
9’ 00”, 2’700m AMSL
*FlyAware is Flyability’s SLAM engine, used in both Elios 3’s piloting app and Inspector 4.0
**FARO Connect is FARO’s 3D mapping software designed for the seamless processing and management of Elios 3’s LiDAR data.
The Standard vs Surveying Configurations
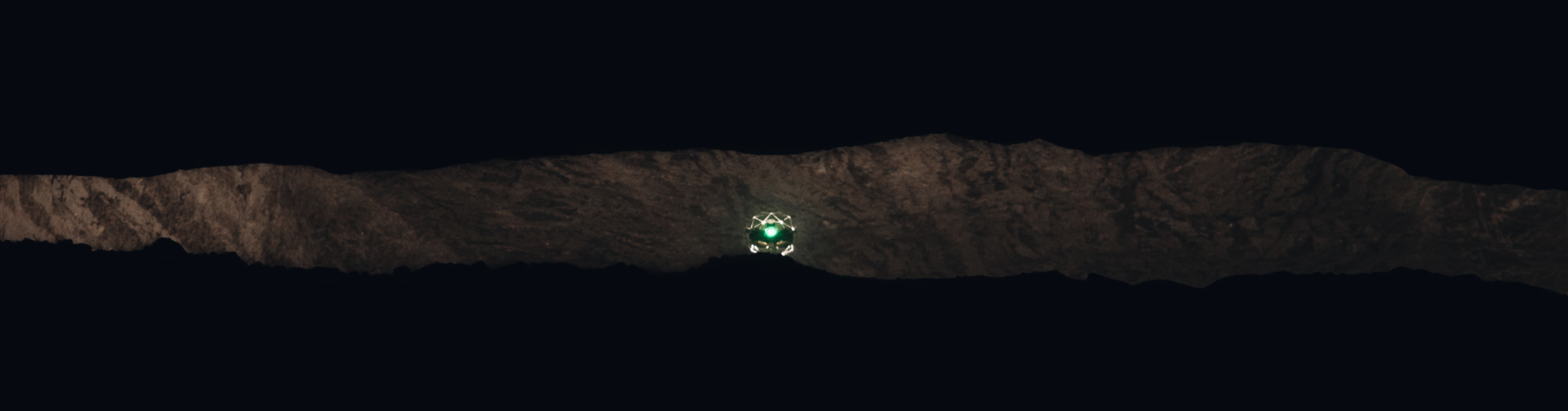
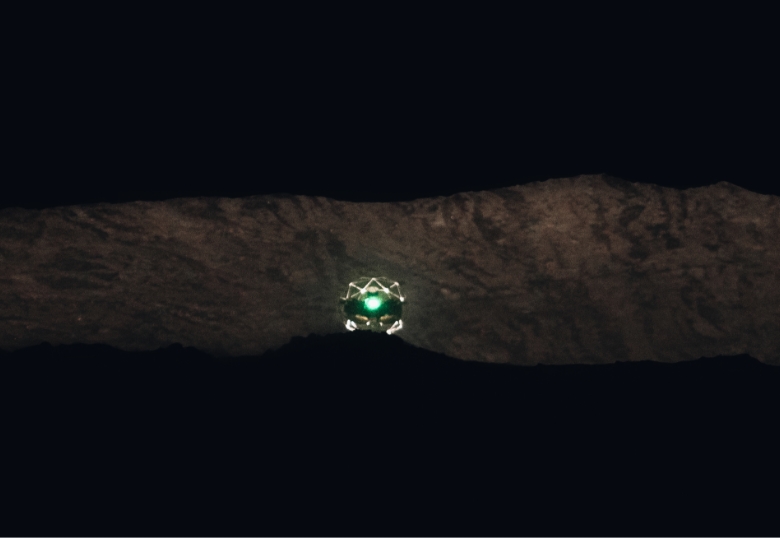
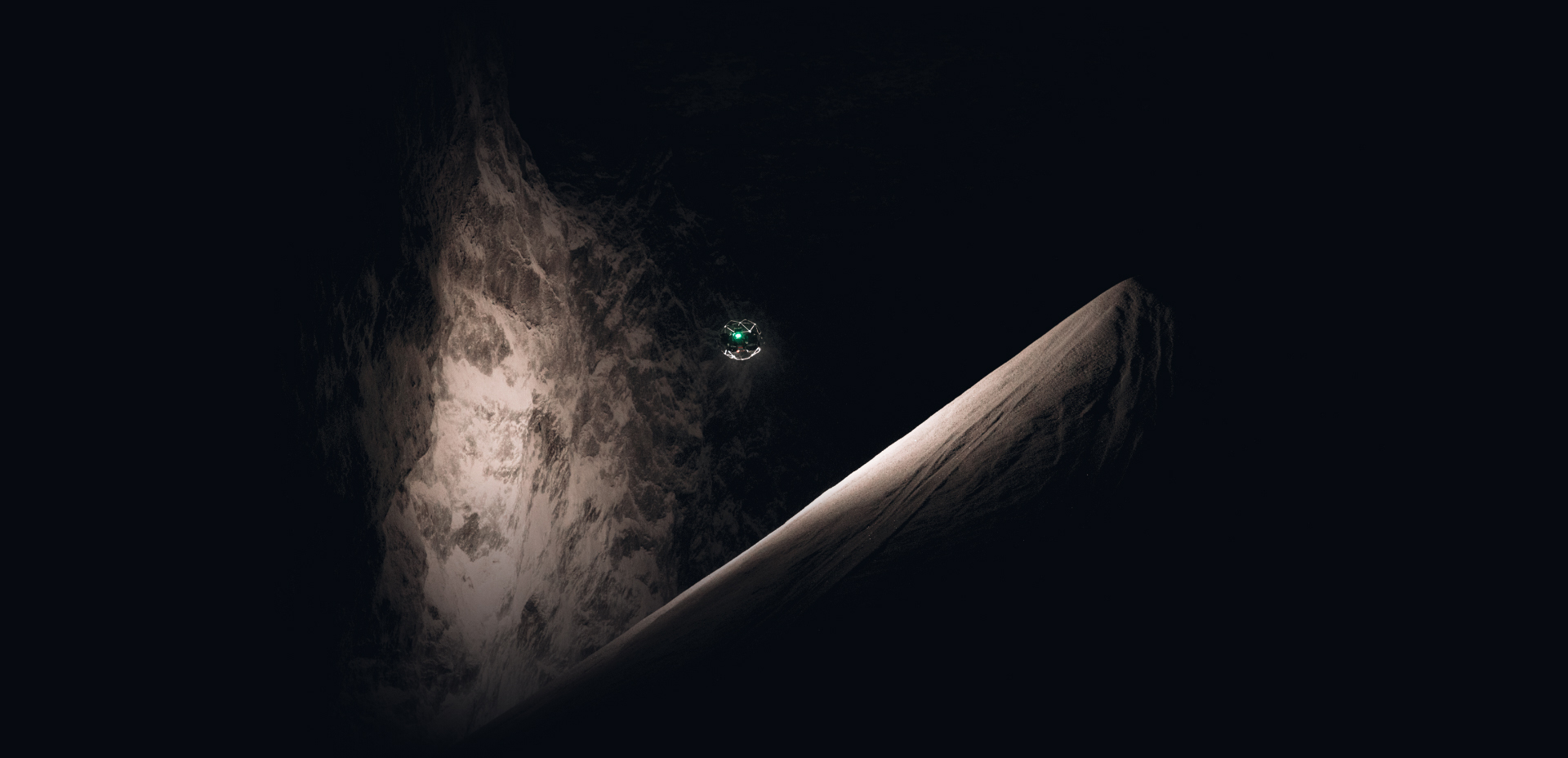
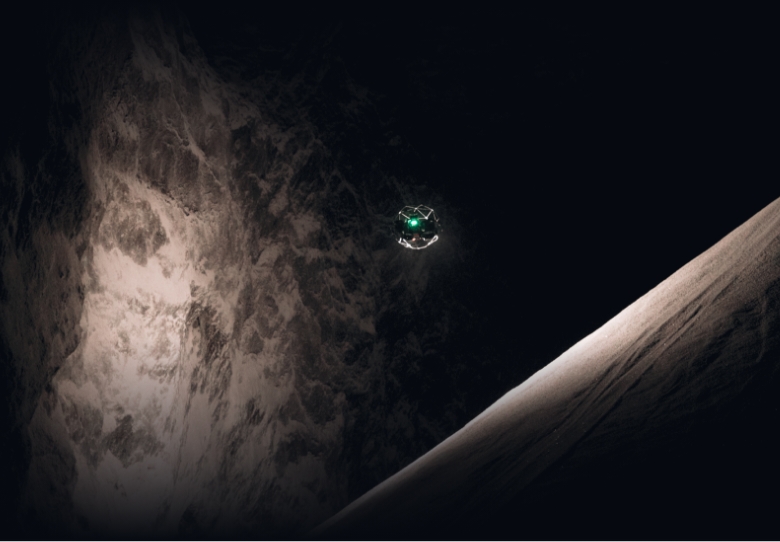
Testimonials
What our customers say about Elios 3 Surveying Payload
“
“The Elios 3 Surveying Payload is a game changer for our operations. It is a tool that we can depend on to capture accurate data day in and day out. We are very impressed!”
Simon Pollitt, Chief Surveyor, ICL Boulby
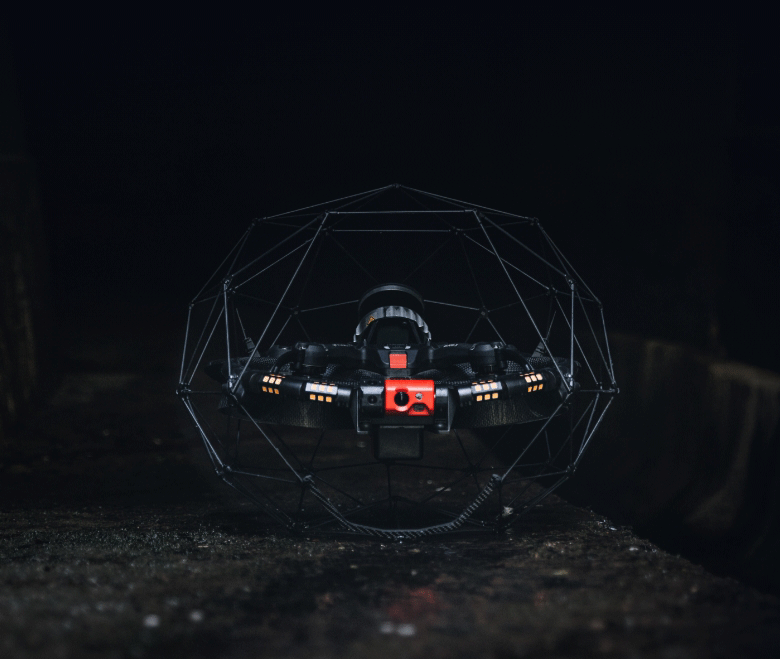