- Blog >
- What Is Turnaround Time? What Is Downtime?
What Is Turnaround Time? What Is Downtime?
Turnaround time is the amount of time it takes to complete a process. One of the most common phrases used for turnaround time is downtime.
An easy way to think of turnaround time is the time from the moment a request is made or a process is started to the time when the request is fulfilled or the process is complete.
In industrial settings, turnaround time is the time an asset like a boiler or pressure vessel must be offline while workers perform maintenance, upgrade the equipment, or make some other kind of important change.
In computing, turnaround time refers to the time from the submission of a process for execution to the return of the output of that process. In warehouse logistics, it refers to the time from the beginning of a process, like the submission of an order, through to its completion.
In warehouse logistics, turnaround time refers to the time from the submission of a fulfillment order to the time when that order has been fulfilled.
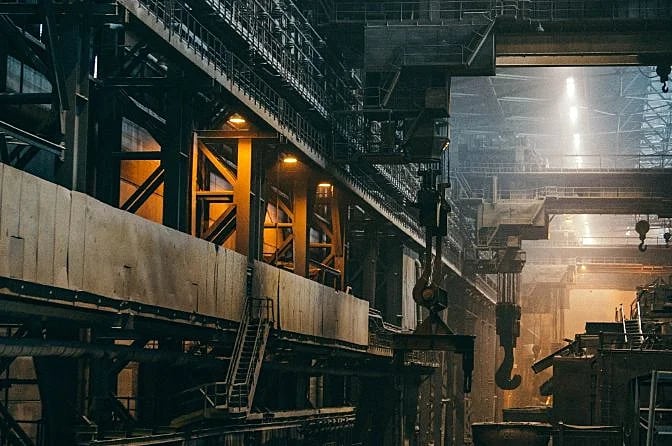
What Does Turnaround Time Mean?
Turnaround time at an industrial plant is the amount of time needed to shut down a specific asset or an entire operation in order to conduct maintenance or some other process.
This period of time is often commonly called downtime, a planned outage, or a plant turnaround.
If the entire plant needs to be maintenanced, turnaround time will refer to the time the plant needs to be down while personnel conduct their maintenance work.
Put simply, turnaround times are periods in which nothing is being done—that is, when whatever a factory or plant typically produces cannot be made because an essential part of the process is offline (or the entire plant is offline, in the case of a plant turnaround).
Turnaround times are typically planned in advance.
But if a plant or operation has a sudden emergency that requires it to be taken offline, then the time personnel need to fix the issue and get the plant or asset up and running again can also be referred to as turnaround time, since it still describes the time needed to complete—or turnaround—the work required to return operations to normal.
During planned downtimes, these are some of the most common types of turnaround work:
-
Regular maintenance. This includes both inspections and any subsequent work performed as a result of the inspector’s findings.
-
Replacements of parts or entire assets.
-
Repairs.
-
Upgrades. These could include upgrades to energy, lighting, parts, or even entire assets in the company’s processes.
-
Unusual world events. This last item covers unique happenings, such as the COVID-19 pandemic, which could require a temporary plant shutdown for personnel to enact new health protocols. The time needed for such procedures to be put in place could be called turnaround time, since it refers to a period of time during which the plant will be off while personnel conduct a discrete process.
Why Turnaround Time Is So Important
In any setting, turnaround time equals money.
Why is that?
Because turnaround time is time in which a plant can't operate, which in turn means that it's time in which you are not able to make money.
This means that the less turnaround time you have, the more potential profit you can make.
In shipping, for example, the faster you can complete deliveries, the more deliveries you can make, and the more you profit.
This holds true in industrial turnarounds as well. The faster you can get your operations back online, the faster you can go back to making a profit.
Take the case of an industry like Power Generation, where the product created is power. Every single minute a power plant is down represents a loss of potential profit, which means that every minute that can be cut off of a plant’s turnaround time represents money that the company has saved.
In fact, for big power plants and other large industrial operations, like oil refineries, even a single day offline can represent tens of thousands, hundreds of thousands, or even millions of dollars lost in a single day.
But machines can’t run all the time.
At some point they need to be inspected and maintenanced, and during this time operations must be paused so that inspectors can safely look at all of the working parts in order to see if any flaws or defects have developed since the last inspection.
Five Steps to Reduce Turnaround Time
Because turnaround times can be so expensive, companies are constantly looking for ways to speed up their processes.
As speed is increased, it’s critical that safety considerations be kept top of mind, and no corners are cut when it comes to taking the proper steps to ensure that no employees are put in harm’s way.
Here are five steps to help improve plant turnaround times without sacrificing safety.
1. Plan Ahead
In the case of plant turnarounds needed for regular inspections and maintenance, these can be anticipated well in advance and thoroughly planned for since they are usually required periodically—annually, bi-annually, or on some other time frame, as mandated by law in many instances.
To improve time for these types of turnarounds, managers can determine:
-
The specific steps needed for the turnaround
-
The scope of the work
-
A detailed schedule
-
Who will be doing what
-
Possible equipment needs
In some instances, doing a dry run may help save time during the actual turnaround period, both by providing practice for the day of the inspection and by helping personnel surface problems in the workflow in advance.
2. Engineering Considerations
If you anticipate needing in-depth engineering work during a planned outage (or are having a turnaround just for this reason), here are some steps you can take to try and avoid unanticipated delays:
-
Identify exactly what will be needed well in advance from an engineering perspective.
-
Ensure any new technology that needs to be put in place works and is on-site, ready to be installed well in advance of the scheduled downtime.
-
Establish a way to test any new technology after it has been installed so that personnel can confirm it's working properly before bringing operations back online.
-
Ensure that the proper personnel will be present to do the work.
3. Schedule Coordination and Communication
Although plant turnarounds can be planned well in advance, this advance scheduling also needs to include communication with other departments in a plant or company.
If all stakeholders aren’t looped in about an upcoming turnaround, the result could be wasted time and energy.
4. Management During the Turnaround Period
When the turnaround begins, it’s crucial that everyone involved knows their job and is moving as efficiently as possible through their work.
Oversight can be key to efficiency during these times. An organized manager can ensure that every individual with a role in the turnaround is on task and has the support they need to complete their job, and that any potential delays are surfaced and addressed as quickly as possible.
5. Post-Turnaround Reporting
Reporting on the success of the turnaround period after it’s complete is an essential part of the entire process.
Through thorough reporting companies can surface problems and address them the next time they have a turnaround, and improve their processes over time.
As part of the post-turnaround reporting, companies can do a review of each person’s job as well as the turnaround period as a whole, meticulously checking to see where there might be room for improvement.
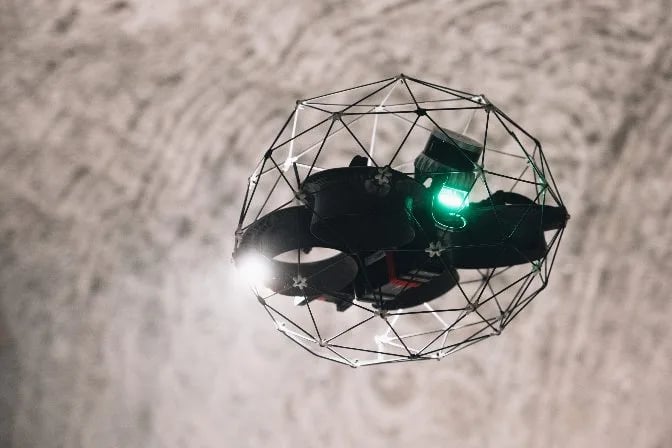
How Drones Help Significantly Reduce Turnaround Times
The five steps listed above can help improve turnaround times overall, but there is also a sixth step you can take, which is incorporating new technology into your workflow to rapidly speed up processes.
And this is where drones come in.
Drones can help significantly reduce turnaround times by making it much easier and quicker for inspectors to collect visual data for inspection purposes.
Here are two of the primary ways a drone like the Elios 3, Flyability's collision-tolerant drone made for indoor inspections, can help significantly reduce turnaround times.
1. Reducing the Need for Scaffolding
Inspections inside of boilers, pressure vessels, or other large, confined spaces require the construction of temporary structures such as scaffolding for inspectors to stand on.
Building and taking down scaffolding for the purposes of an inspection can take weeks. Using a drone, inspectors can fly into a boiler, collect the visual data they need, and exit without the need to build anything at all, completely removing the days of extra turnaround time required for those manual supports.
Of course, maintenance crew will still need to use scaffolding in order to perform any repairs that might be needed.
But the visual data the drone provides can significantly reduce the overall need for scaffolding by pinpointing the exact location where scaffolding needs to be built for repair work and avoiding the need to build it throughout the asset.
2. Speeding Up the Collection of Visual Data
An inspector standing on scaffolding or even just walking around the inside of an asset with a flashlight typically moves much more slowly than a drone flying through the asset filming it.
One customer recently told us that our second generation drone, the Elios 2, collected visual data for an inspection of a key component in their power generation work in a third the amount of time it would have taken an inspector to do it. The drone completed the work in just 10 hours, while it would have taken 30 hours if done manually.
And that turnaround time reduction of 20 hours represented significant savings for the Power Generation company.
As you can see from the examples above, using a drone for inspections not only helps reduce turnaround times, it also helps improve safety and save money.
Below are some case studies highlighting these additional benefits, with a focus on ways that the Elios 2 and Elios 3 have helped companies increase safety and savings—in some cases, millions of dollars—by significantly reducing their turnaround times.
-
Elios 3's 3D Mapping Helps City of Lausanne Water Department Inspections
- Drone reduces time needed for Scrubber inspections by 98%, saving 470 hours of work
-
Saving over $1 million with the Elios 3 for wind turbine inspections