Know exactly where to act and the conditions you will face before entering an asset
Sending an inspection team to assess the conditions of an asset is not only dangerous but also time-consuming and expensive. Using a nuclear inspection drone will allow you to avoid unnecessary human exposure to radiation, improve decision-making, and reduce inspection time and cost.
By deploying the Elios 3 RAD, you can collect visual, LiDAR, and radiometric data without having to send humans or install expensive and inefficient radiation-hardened cameras. The RAD Payload, developed in collaboration with Mirion Technologies, allows you to accurately estimate the current and cumulative dose exposure a person would face in every corner of your asset and thanks to the high-quality data collected by the drone you can understand if there is a need to intervene and exactly where and how to act. The Elios 3 was successfully tested in 10,000 R/h conditions and all its components continued to function perfectly after an accumulated dose of approximately 4,000 R.
-
Image represents: LiDAR and radiometric data collected inside a turbine room using the Elios 3 RAD.
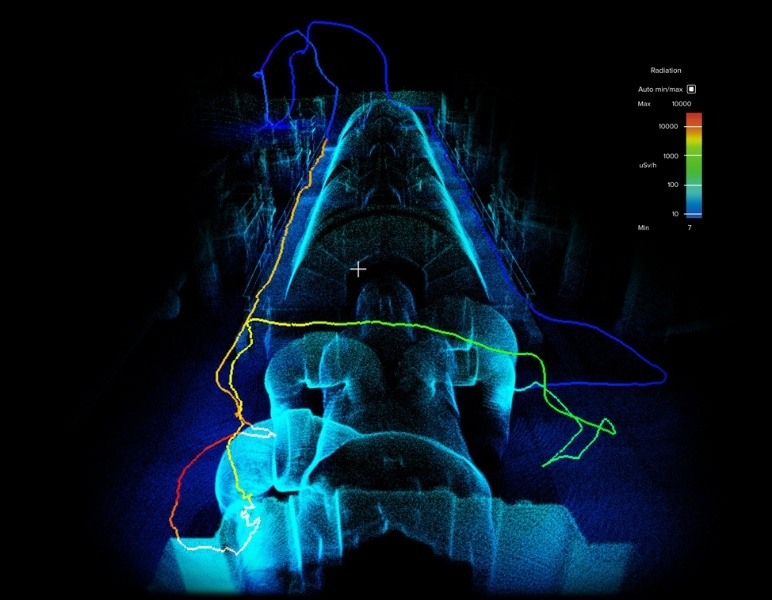
The benefits of adopting remote drone inspections in nuclear
Safety
Perform remote inspections and collect current and cumulative dose data for efficient dose planning.
Efficiency
Increase efficiency thanks to a faster deployment, an always on-site solution, and live-data results.
Downtime
Cut costs and asset downtime by inspecting entire assets in a team of just two while the plant is live.
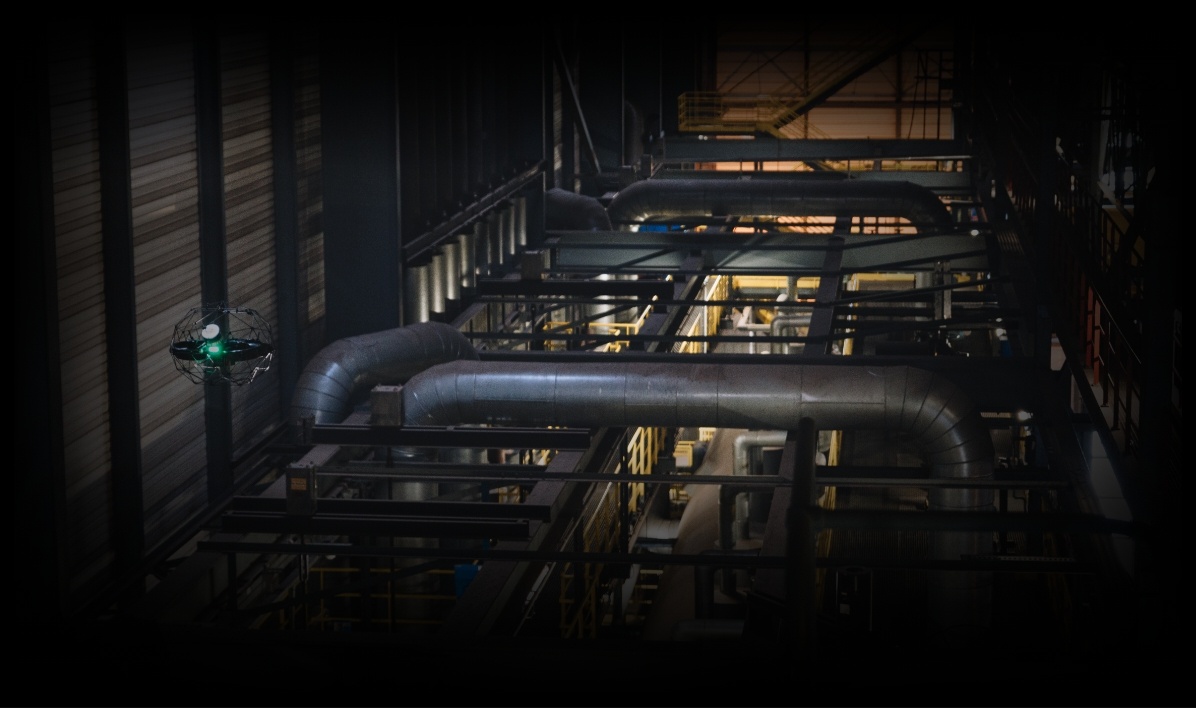
Collect data safely and efficiently in the nuclear industry and boost productivity
Explore a wide range of nuclear inspection drone applications
-
Nuclear condenser inspection
Read moreInspecting a condenser using traditional techniques can take up to 14 shifts of 12 hours just to build the scaffolding, costing the power plant well over $100.000 per condenser. Not to mention the safety concerns that come with having people work at height and introducing foreign objects inside the condenser. The Elios 3 drone is ideal for this type of confined space inspection. You can perform a complete structural assessment, look for corrosion and cracking, and even perform UT measurements of the shielding, pipes, and other sections of the asset.
-
Nuclear waste management
Read moreRevolutionizing Nuclear Waste Management with the Elios 3 RAD Drone. In this exclusive interview, Kevin Young from the U.S. Department of Energy (DoE) and Amanda Smith from Sellafield discuss how this nuclear waste management drone, the Elios 3 RAD, is transforming operations at nuclear waste facilities.
-
Turbine deck inspection
Read moreQuickly deploy the Elios 3 RAD from a convenient area without the need for complex safety procedures to identify, locate, and monitor the radiological conditions of an asset. Get 100% data coverage even in no-go zones and avoid exposing workers to hazards and unnecessary dose rates.
-
Irradiated storage vault mapping
Read moreElios 3 RAD was used to create a 3D model of a calcine at the Idaho Nuclear Technology and Engineering Center, enabling nuclear waste extraction planning. Elios 3 RAD was the only tool that could provide 100% accurate data of the vault and it only took 7 min to 3D map the interior of the vault while meeting the IEC’s accuracy needs.
-
Nuclear decommissioning
Read morePersonnel at a decommissioned power plant owned by Vattenfall used the Elios 3 to create 3D models inside a "no-go" zone, improving their understanding of an area where it wasn’t safe for people to enter. The Elios 3 allowed the team to remotely assess the condition of an asset in minutes and collect the necessary data with a team of just two.
See how Elios 3 RAD helps our clients save time, money, and stay safe
“
“[By using the Elios 3] I see a financial gain because we don't mobilize resources to feed, for example, a 10m high scaffold. [ ] Sending people is obviously an additional cost and what's more these activities are outsourced. The advantage of having this drone at our disposal would be to re-internalize this type of inspection, in order to optimize inspection time.”
Anthony Rampello
Inspection Manager, EDF Cattenom
They already use our products