INDUSTRY 4.0
Get ready for a new era of internal inspection and mapping
Drone-based inspection is not a technology of the future, it is a necessity for today’s digital fast-paced world. With the 4th industrial revolution in motion, organizations are looking to deliver digital transformation of their industrial processes, while cutting costs and bettering workers’ environments.
Elios 3 helps industrials effortlessly achieve these goals by bringing their inspections and mappings to the next level.
Much more than a flying camera, Elios 3 is a powerful data-harvesting tool.
Relying on the power of computer vision and LiDAR mapping, Elios 3 is a versatile indoor drone opening doors to a world where performing systematic inspections does not require months of training, reporting is done intuitively on a 3D model of your asset, and situational awareness is built into the piloting app.
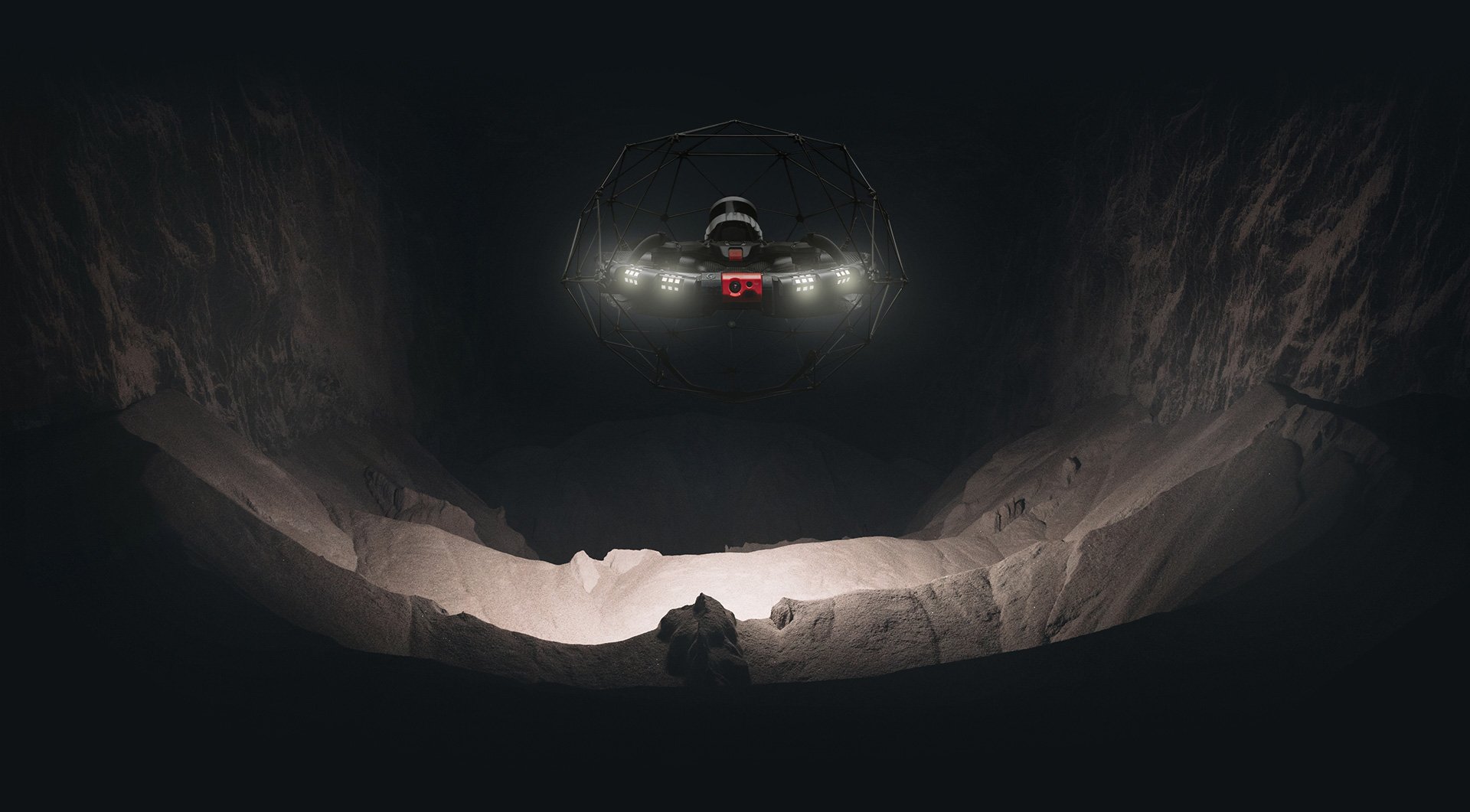
FlyAware™ SLAM Engine
Powered by FlyAware™.
FlyAware™ is the unique combination of computer vision, LiDAR technology, and a powerful NVidia graphic engine. Acting as a centimeter-accurate indoor GPS, it builds real-time 3D maps enabling the drone to sense its surroundings instantaneously. Today, Flyaware™ allows for groundbreaking stability and highly accurate locational awareness. Tomorrow, it is the promise of complex confined spaces inspections performed in full autonomy.
SLAM-Based Stabilization
Stone-still stability. No matter the conditions.
The all-new SLAM-based stabilization algorithm catches the tiniest unpredictable movements of the drone and instructs the flight controller to compensate for it. This allows for the drone to float in the air still as a stone even in the toughest conditions. With Elios 3, pilots from all skill levels will succeed at performing complex missions with close to no training.
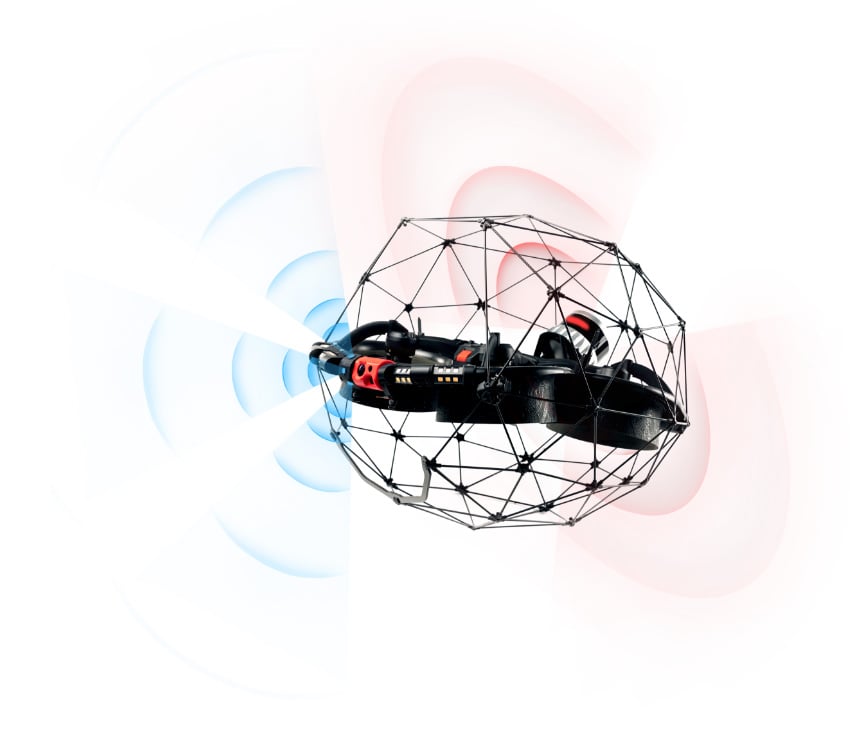
3D Live Map
Flawless locational awareness.
The embedded LiDAR constantly scans the surroundings to build a high-density point cloud map. This map is displayed instantly in the Cockpit App, empowering pilots with exceptional locational awareness. A real-time 3D view of the drone’s trajectory and environment provides crucial data.

Always know where you are.
The drone’s position is located precisely so the pilot can easily decide on the optimal route to safely return home.

Assess inspection coverage.
Cumulative mapping data shows the completeness of the map so you can instantly assess your inspection coverage.
Modular Payload Bay
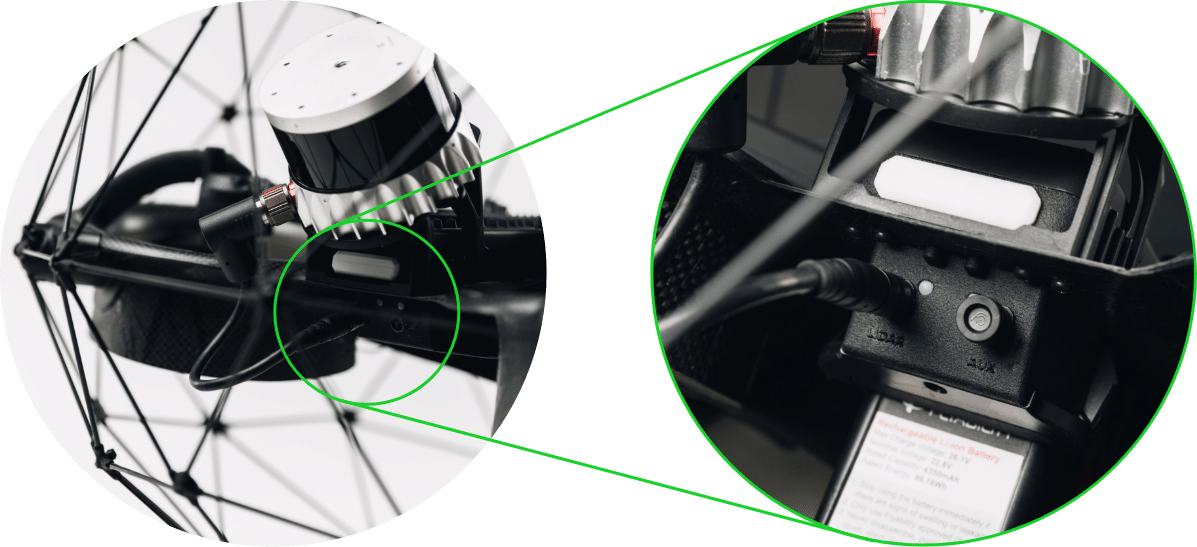
A versatile and future-proof inspection tool.
The modular payload bay features two ports. One dedicated to the LiDAR and one for auxiliary payloads. This unique integrated design provides aerial capabilities for a range of upcoming indoor applications. It turns Elios 3 into a versatile, future-proof tool, configured to fit your mission needs.
Available payloads
HIGH PRECISION LIDAR DATA
Elios 3 Surveying Payload
Surveying the inaccessible
PRECISE RADIATION SENSING
Elios 3 RAD Payload
Remote radiation detection and localization
Return-To-Signal
Enhanced flight safety
The Elios 3 automatically monitors the live video connection. When the video feed is interrupted, the drone prompts a popup in Cockpit, offering to autonomously return along its original trajectory until the video connection is restored.
The Return-To-Signal feature provides added peace of mind for the pilot to explore further away even in marginal radio signal conditions.
Collision-Resilient Rugged Design
Ready for the tough work.
Designed after Flyabilty’s patent-pending collision-resilient flight controller, Elios 3 is fit for use in the most complex industrial settings. With its signature cage and unique reversing motors, Elios 3 is the only drone in the market that can recover from flipping upside-down without crashing. The rugged IP-44 design allows for the inspection and mapping of harsh environments without concern for water splashes and dust.
*Elios 3 is not certified IP-44 but it has been designed to comply with such rating according to the ingress protection code.
Close-Up Inspection Dedicated Payload
Supercharging data quality.
The static payload now comes with a fully unobstructed 180° field of view to a 4K camera, a thermal camera, and a distance sensor. The lighting system has been rethought from the ground-up to bring an even more powerful and homogeneous lighting experience. Thanks to the industry-leading oblique and dust-proof lighting system, looking for pitting, cracks, or build-ups becomes as natural as doing it manually with a flashlight. Elios 3 close-up inspection payload delivers stunning image quality, consistently smooth, even in the complete dark.
Ingenious lighting system
Dust-Proof 16K Lumen Lighting
Traverse dusty place without losing sight of your objective
Extended Air-Time
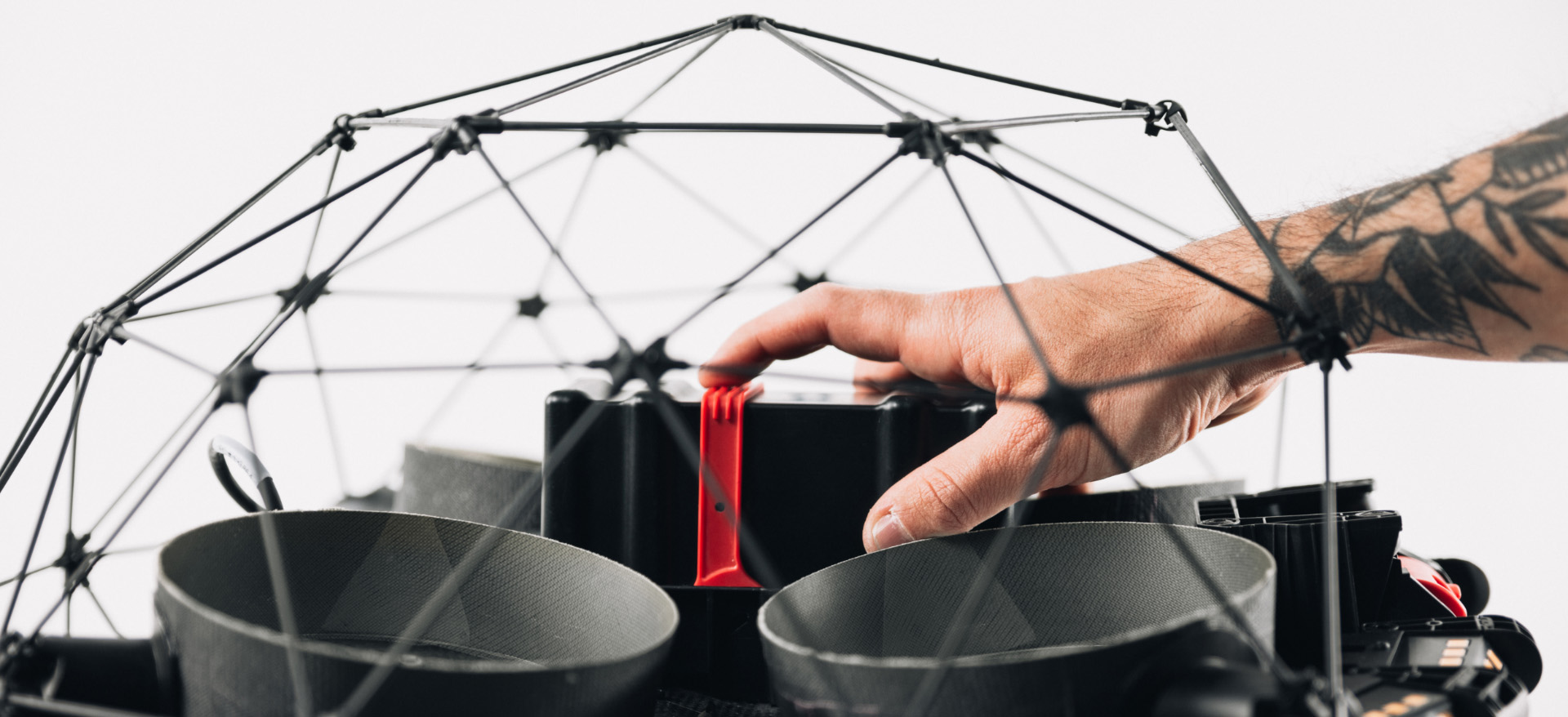
Do it all in one go.
The Elios 3 offers up to 12 minutes of flight time* so you can go the extra mile in every single flight. With a new insert & lock mechanism battery manipulations are easier than ever.
*Flight time without a payload mounted on the payload bay.
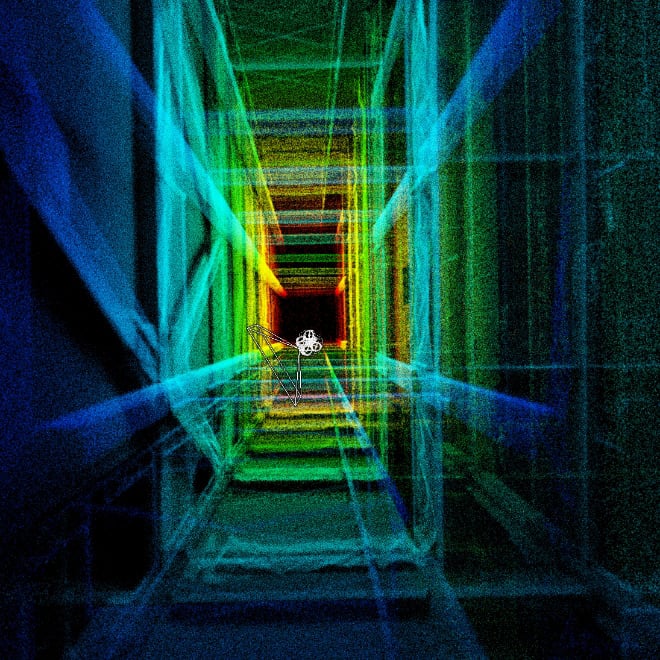
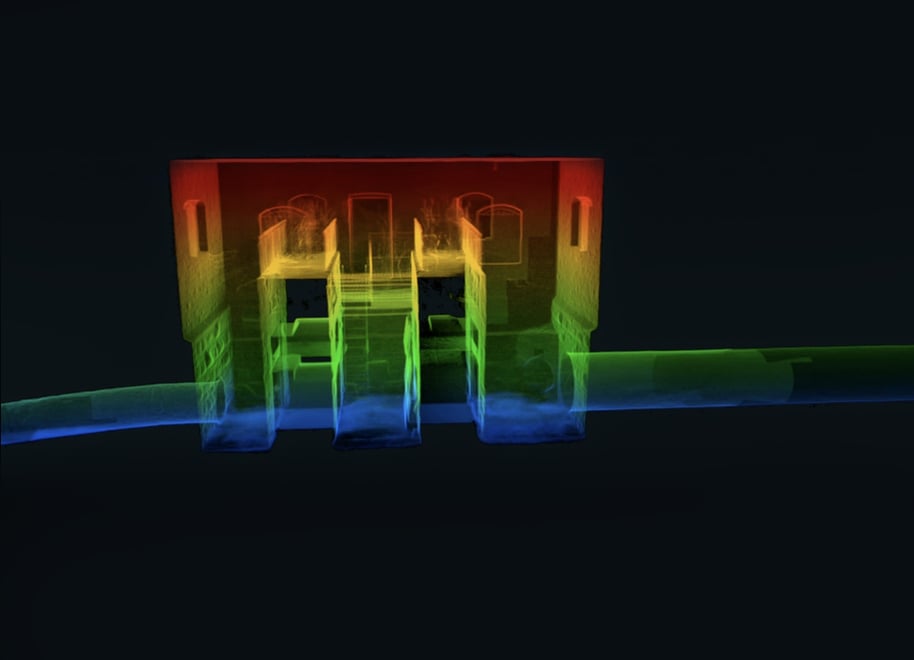
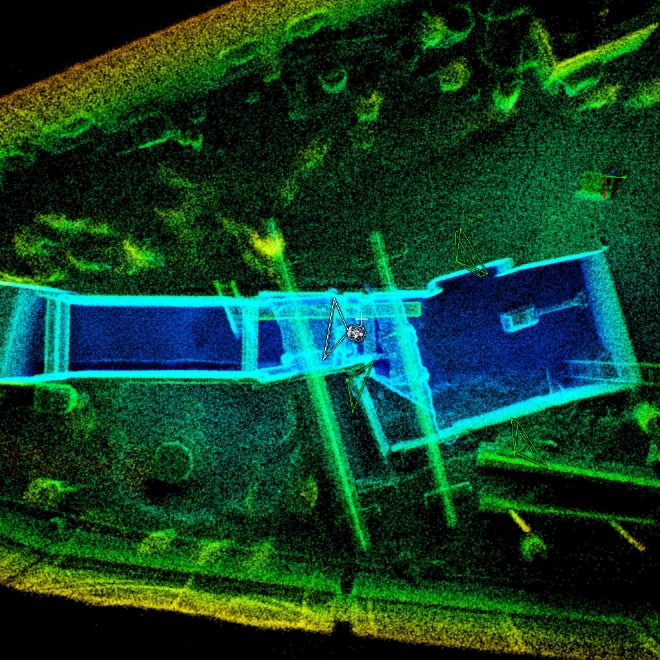
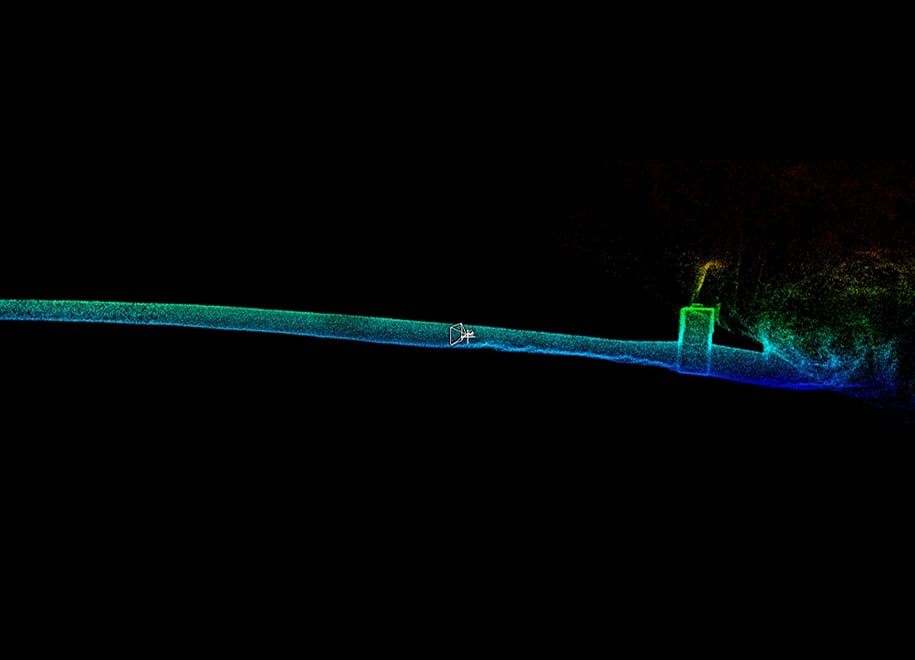
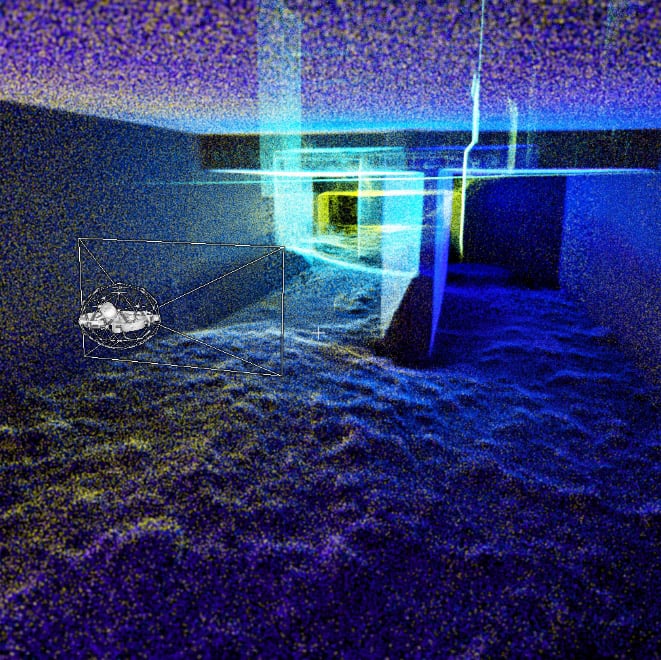
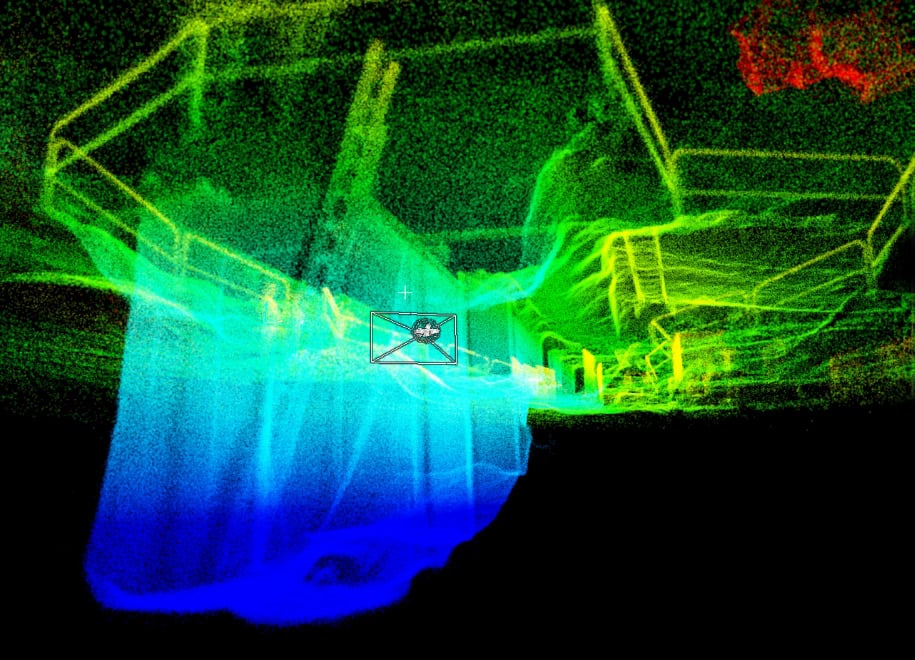
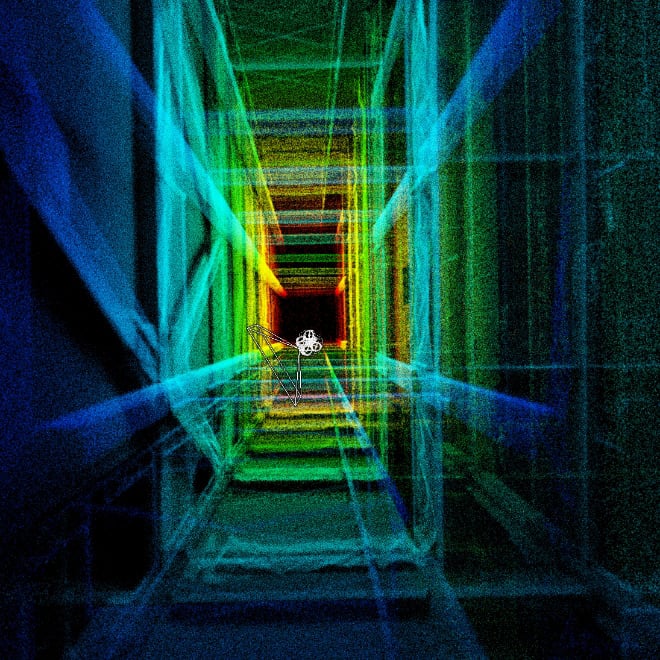
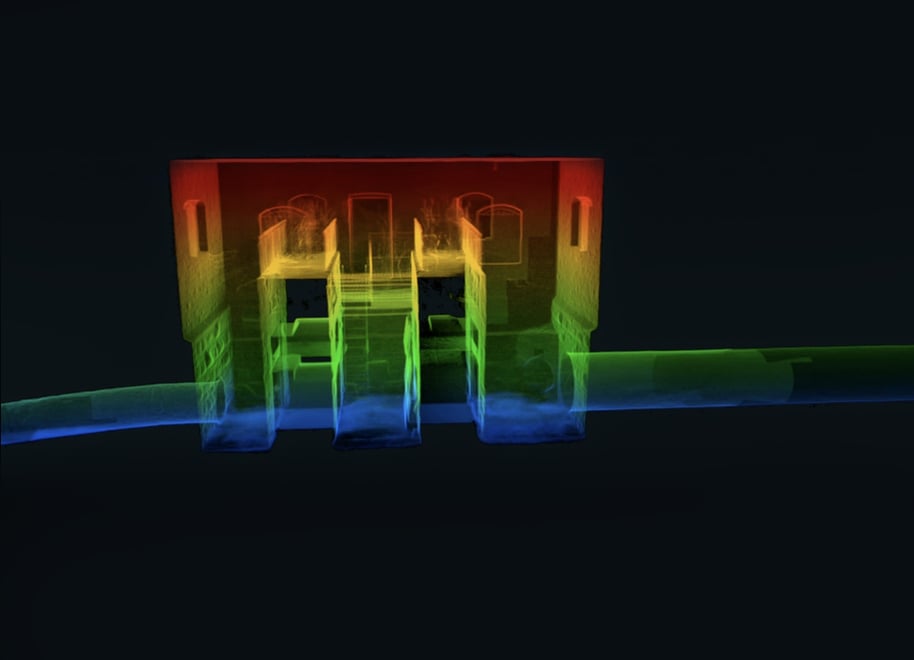
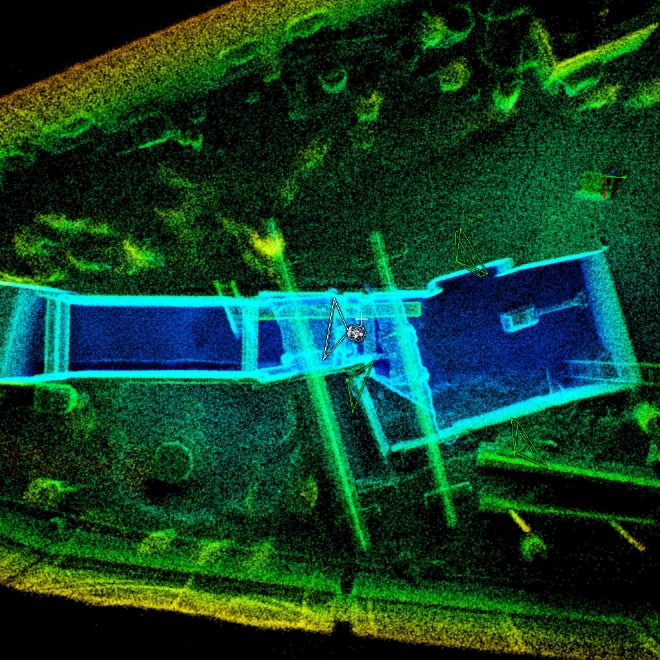
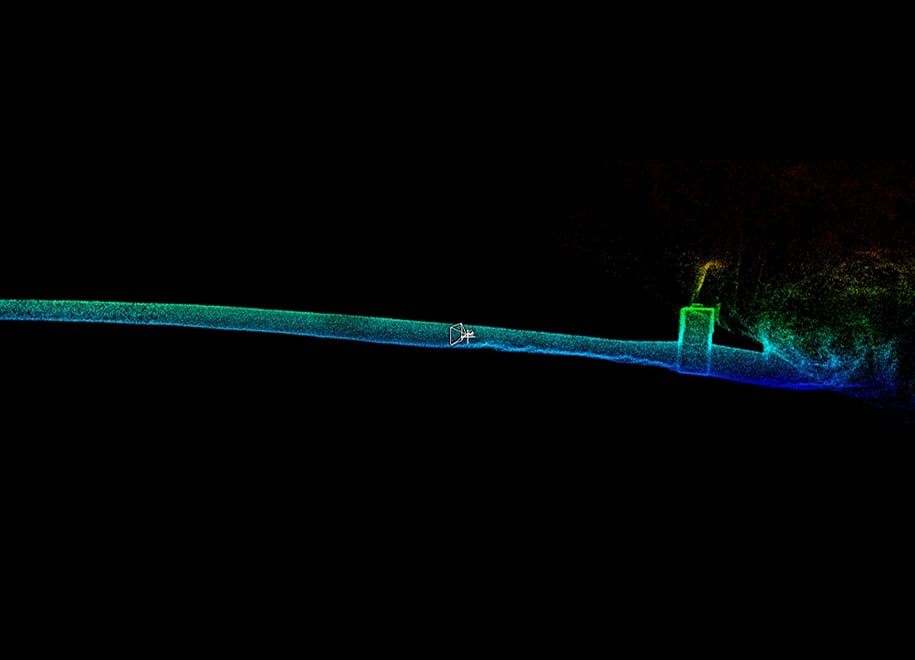
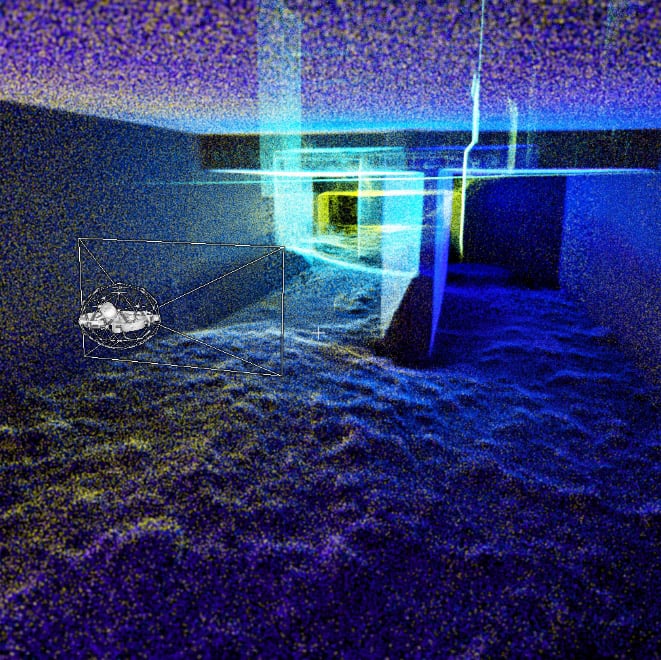
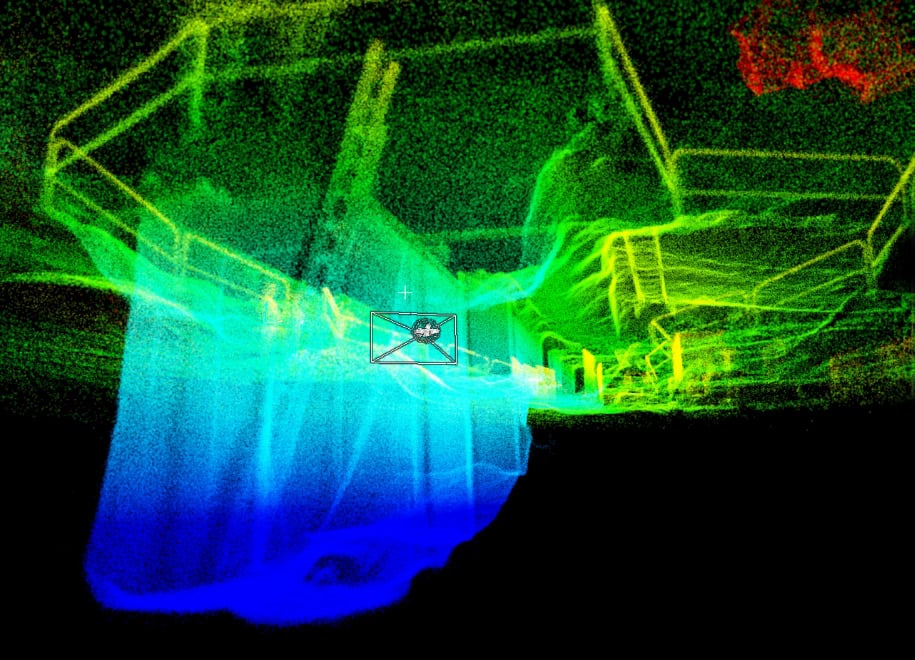