- Case Studies >
- A drone stack inspection with the Elios 3 UT
A Drone Stack Inspection With The Elios 3 UT
The Elios 3 UT flew inside the stack, cutting the need to affect insulation on the outside, producing accurate results that can be repeated for routine inspections.
Benefits In A Nutshell
Access The Elios 3 could fly inside the stack, rather than outside. There was no need for specialists to remove insulation on the structure when the drone could fly inside. |
Safety No work at height was required, and the team were able to conduct flights from inside a warmed area, rather than working outdoors in the cold. |
Adaptability The Elios 3 UT could be used beyond the line of visual sight to get UT measurements inside the asset where an external inspection wasn't possible. |
Reporting The measurements were clear and provided knowledge about the state of the stack that can be used for record keeping and planning future maintenance work.
|
Industrial stacks face a variety of inspections to ensure they are safe for operation. Visual inspections are performed on a regular basis up to several times per year. A full inspection that includes interior and exterior structural analysis is typically conducted every 3 to 5 years. These routine checks on stacks empower preventative maintenance as well as the early detection of faults.
A visual inspection that identifies a potential fault, such as corrosion or cracking, will trigger a more detailed analysis. This is where ultrasonic testing, or UT, is brought in. With an ultrasonic thickness measurement (UTM), the asset manager can better understand the condition of the stack and compare this to existing records as well as industry standards. An accurate UT inspection can determine whether an asset is safe to operate or if urgent intervention is required.
Why A Service Provider Used A UT Drone Inspection
Osprey Integrity offers a range of UAV services that reduce operational risks and offer considerable economic savings to their clients. Their work includes major asset inspections for asset owners like BC Hydro, Suncor, Cenovus, Canadian Natural Resources, and Holcim across Canada and the USA. In 2023, Osprey Integrity was asked to assist with an inspection of an industrial stack.
The stack was at an oil and gas facility in Northern Alberta that is managed by Canadian Natural Resources Limited (CNRL). The stack was the outlet for a once-through steam generator (OTSG). Water is forced through tubes inside the OTSG by a boiler feedwater pump. Once inside the OTSG, the water is converted to superheated steam. The stack serves as the exhaust for excess or waste gas and can reach temperatures of 180 degrees Celsius (350 Fahrenheit).
The stack being inspected was one of these columns, each of which has protective insulation
Because these stacks are insulated, Osprey Integrity conducts a visual internal inspection (VI) of the stack using Elios 2 or Elios 3. The VI can identify indicators of degradation, such as dew point or general corrosion that may be otherwise missed when only conducting a visual external inspection. These findings may indicate an unsafe condition and require quantification to determine the level of risk.
The insulative material is used to manage the stack’s temperature and condition which is particularly important in the extreme climate in Alberta. A traditional ultrasonic testing procedure would require a certified insulation specialist to be lifted up to the stack with a crane (or aerial work platform), where they could strip away the insulation. A certified UT technician would then be called in and carried up with the crane to take the measurements before the insulative material was replaced.
Alternatively, a UT drone inspection with the Elios 3 would be able to gather the data from the stack by flying inside the stack rather than collecting data from the outside. This is what Osprey Integrity wanted to put to the test.
Thanks to the Elios 3's camera, it is possible to complete UT inspections beyond the visual line of sight. The Cockpit app can also be used to manually adjust the gain and gates, as shown on the left side of the screen here.
Ultrasonic Testing With A Drone Step-By-Step
The key for this project was to show the client how a UT drone inspection would compare to the established ultrasonic test procedure. The Elios 3 and its UT payload needed to demonstrate an alternative method with enough benefits to justify turning to drones for at least some UT gauging.
The Elios 3 was able to fit inside the asset, flying in from an access point above the convection section, and up through the stack. This already cut the need for a crane or mobile elevated work platform (MEWP) and removed any need for a person to work at height.
The Elios 3, equipped with its UT payload, flew inside the stack through this small access point
Once inside the stack, the drone pilot navigated to the level where they were concerned about the condition of the stack. From the inside, the Elios 3 started taking measurements. The Elios 3 is designed for withstanding contact - making it the ideal drone for taking UT measurements. The probe successfully took measurements at 4 points in the cardinal directions. This was incredibly efficient - especially as the drone can complete 4 UT measurements per minute made possible through a comprehensive system design, including couplant delivery.
The UT probe used in this project was a prototype of the final Elios 3 UT payload, but features a similar magnetized probe hood that helps the payload affix to the test site - in this case, the inside of the stack
After the flight was completed, the pilot guided the drone back to the takeoff location and the results were quickly provided to the client. The entire process took less than 60 minutes, a fraction of the time it would take with cranes and did not require any unnecessary disruption to the insulative layer on the stack’s outside.
What Are The Benefits Of An Ultrasonic Drone Inspection With The Elios 3 Ut Payload?
Osprey Integrity highlighted several key features from the Elios 3 that empowered a fast and effective UT inspection that outstripped traditional methods.
- The repeatability. This measurement process was fast and resource effective, but could clearly be repeated many times. The drone pilot tagged the location of the measurements in the Elios 3’s point cloud, enabling a fast and easy return to the same measurement point in the future. In the long term, repeat measurements will help the team calculate the corrosion rate and effectively manage the stack’s condition and maintenance requirements.
- The real time viewing interface, in addition to a full recording (4 x second) of the ultrasonic A-scan. Having the ability to see the soundwave during contact allows the UT technician to ensure a suitable contact location and waveform response in accordance with their training. More impressive however, is the ability to review and AMEND measurement specifics in the event an inaccurate thickness value is accidentally captured, preventing the need to omit it from the data, or return to the asset for re-inspection.
- Enhanced access. The Elios 3 reached a space that no other solution on the UT market can currently reach with the same ease and speed. Its ability to work in confined spaces and withstand contact while capturing UT measurements and simultaneous LiDAR and visual data makes it a powerful tool with very few limitations to where it can go in confined or hard to reach spaces. This also unlocks further applications at the same site, not to mention across further industries.
- Unique design. Not only is the Elios 3’s collision tolerant design an asset, but the UT probe itself provides a lot of flexibility. With several options for UT transducers as well as the adaptable arm the payload is mounted on, pilots can adjust their set up according to the UT measurement points size and position. This meant that Osprey Integrity felt confident they would be able to secure the necessary ultrasonic thickness measurements with a drone on their first attempt, which they did. They could also position the probe under the guidance of the Elios 3’s laser pointer, ensuring they gathered UT measurements from the correct location. Finally, the control of the pilot, who can adjust the gain and gates of the measurement in-flight, ensures that the ultrasonic test data is collected correctly, ensuring the success of the mission as it happens.
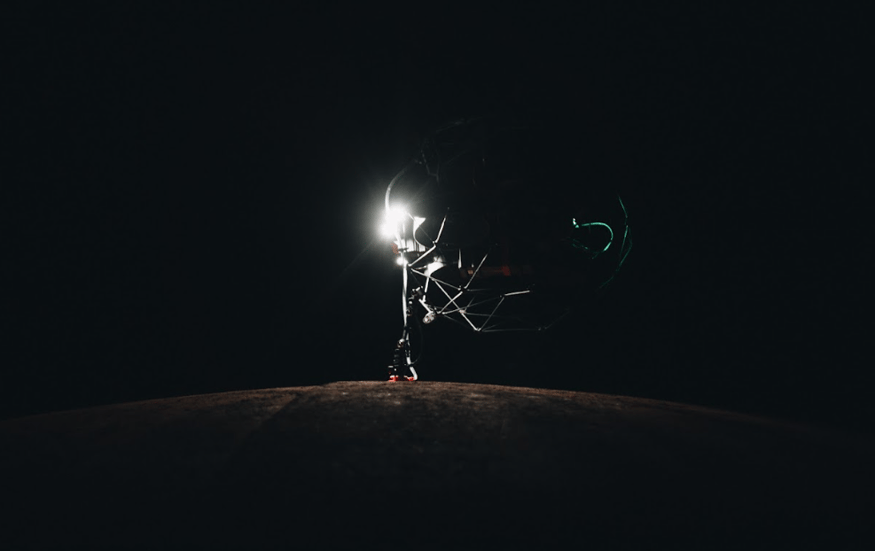
Learn More About The Elios 3 UT Payload
The Elios 3 UT payload was launched in March 2024, with deliveries expected for later in the year. It presents a powerful tool that can enable safety improvements along with cost and time savings without compromising on data accuracy. Moving forward, this payload will add to the capabilities of the Elios 3 and enhance its value for non-destructive testing.
Osprey Integrity recently presented at Flyability's User Conference in March 2024, where they shared their experience with the payload in its testing phase and the way it impressed CNRL with the first mission. Osprey Integrity has been operating drones for UT inspections for two years already, and their approval of the Elios 3 UT payload highlights the way this device represents an exceptionally exciting and capable addition to drone NDT across multiple industries.
Discover more about the Elios 3 UT payload